PACKAGING AND SHIPPING EQUIPMENT
General Kinematics offers industrial shipping and packaging machinery to suit wide and varied operational and logistical needs of many types of organizations. From densification of small pallets to entire over the road trailers, GK uses vibration to maximize the volume of the container you are filling. And when it is time to get the material back out, GK can help with that too. Maximize your material handling with GK’s industrial packaging equipment and shipping machinery.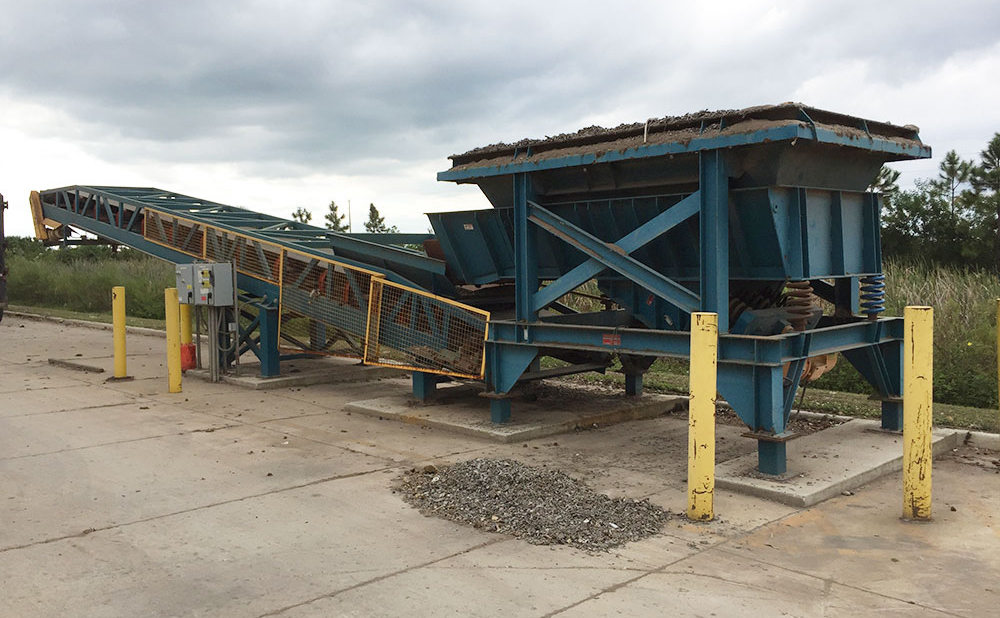
LOAD-RITE? CONTAINER LOADING SYSTEMS
Minimization of empty container space is important to maximize your profitability of each container load.
GK’s LOAD-RITE? Container Loading Systems allows you to maximize the shipping weight of your container from back to front. Material is directly loaded onto GK’s heavy-duty PARA-MOUNT II? Vibratory Feeders, and is evenly distributed onto a belt conveyor which is inserted into your container. As the truck slowly pulls forward, the belt continuously feeds the container until it reaches the maximum volume.
FERROUS SHRED:
20’ or 40’ Overseas Containers
Fill 45,000 lbs. in under 10 minutes
Standard size hopper to suit bucket loader
Vibratory Two-Mass Feeder to minimize bridging and bulky eliminate piles
Gentle transition onto high speed belt conveyor
Optional belt scale for precise control
FEATURES:
Heavy-Duty feeder withstands heavy impact
Low horspower design reduces energy requirements
Systems are available in fixed and skid mounted designs
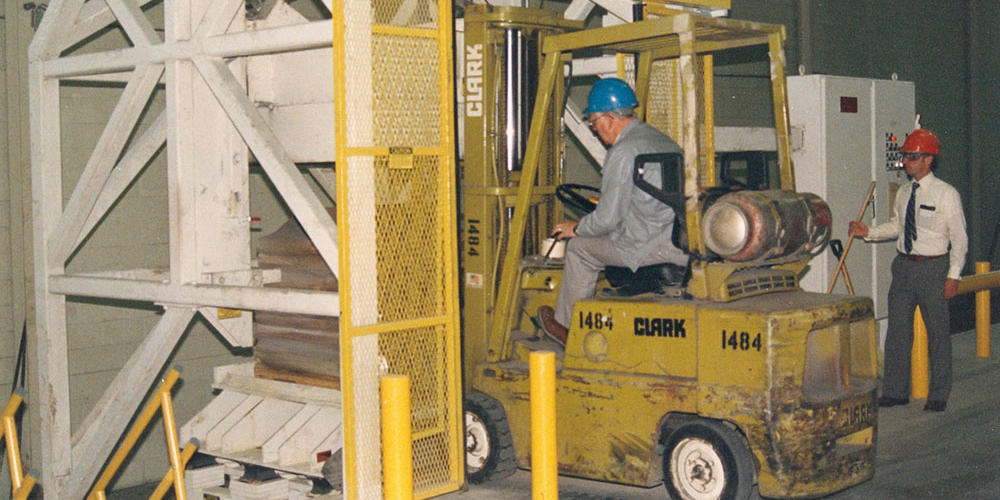
VIBRA-BUSTER? VIBRATORY LUMP BREAKERS
The General Kinematics VIBRA-BUSTER? Vibratory Lump Breakers breaks up settled material through vibratory activation. From a single bag to an entire pallet of material, the VIBRA-BUSTER? energizes material to separate clumps and settlement without product degredation.
FEATURES:Break up lumps in settled material without effecting product quality.
Minimal energy required to operate system, and few moving parts for low maintenance.
Can be loaded by hand or with equipment.
Systems are custom designed for your particular material and process for optimal results.
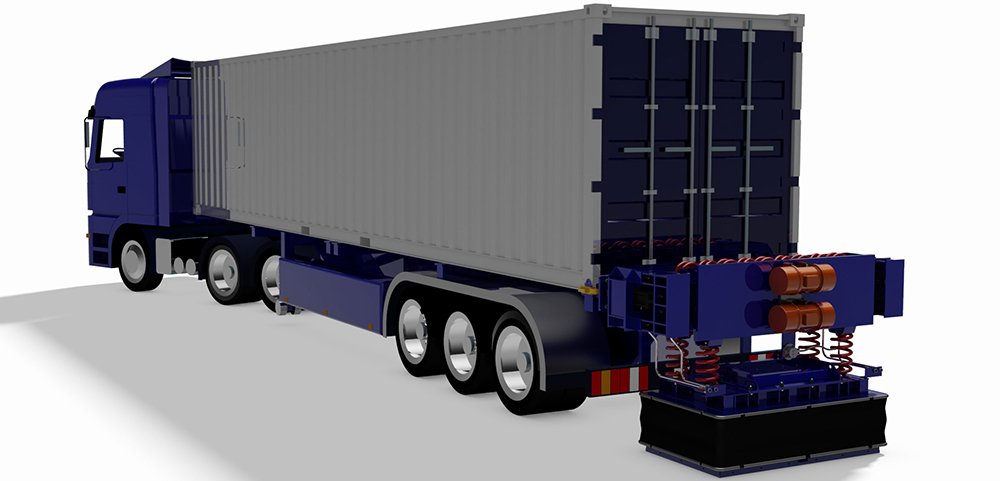
VIBRA-PACK? SHIPPING CONTAINER DENSIFIER
The VIBRA-PACK? fills the full volume of your bulk containers to:
Move bigger payloads.
Use fewer containers per order.
Dramatically reduce total shipping costs.
Attaches directly to container on trailer, no special containers or equipment needed.
Manual or hydraulic clamping available.
Optional scissors lift for height adjustment to match a variety of trailer configurations.
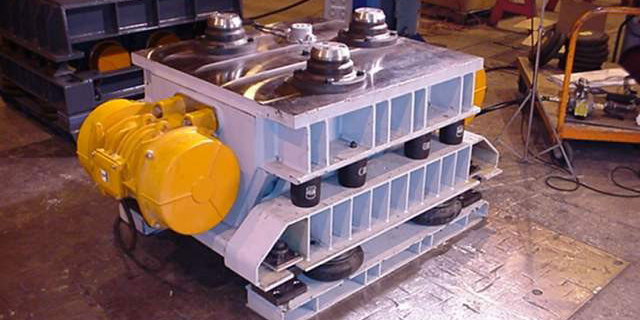
COMPACTION TABLES
The constant controlled agitation produced by General Kinematics Vibratory Compaction Tables optimizes product densification to eliminate settling during transportation. Vibrating compaction tables are available in a full range of sizes with various control and operating features tuned to your specific product and process
FEATURES:Low profile, compact, single-mass systems ideal for use with roller conveyor lines.
Rugged Two-Mass tables capable of compacting up to 50 ton loads with less than 10 horsepower.
Load sensing feature available to automatically compensate for change in product weight.
Fully sealed motors and drive system to minimize maintenance.
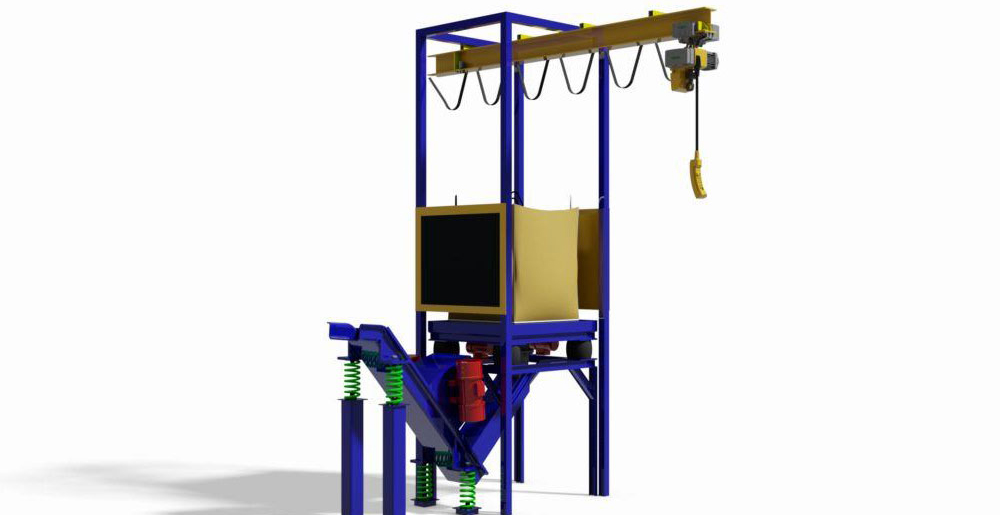
VIBRATORY BULK BAG DISCHARGERS / CONDITIONERS
General Kinematics Bulk Bag Dischargers / Conditioners help unload stubborn or settled product from bulk bags. Utilizing vibratory action, material is excited to dislodge and break apart clumps and sticky product. Material flows through bottom chute, and can be discharged into a variety of conveying devices. Bag dischargers are available with a variety of options and accessories. Contact a GK Product specialist for more information.
FEATURES:Bags can be loaded using a forklift, or GK can design custom hoist frames and other accessories to automate your process
Optional custom control systems can be designed to regulate flow and volume.
Available in mild or stainless steel.
Standard and custom sizes available depending on your application.
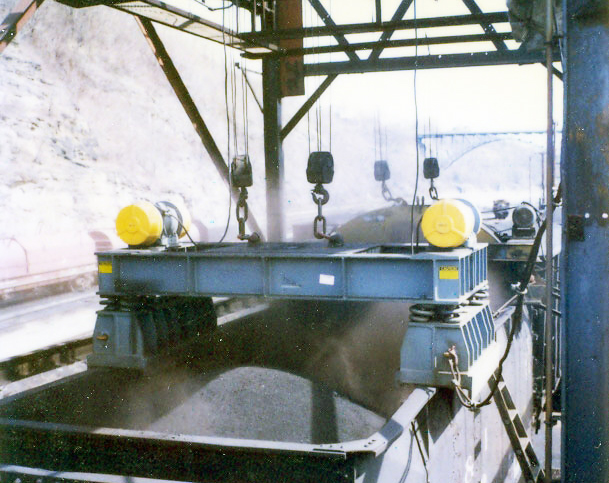
HIGH PERFORMANCE CAR SHAKEOUT
Engineered for fast cycling, General Kinematics Rail Car Shakeouts are equipped with twin, self-contained vibratory drives mounted on a rigid, reinforced exciter frame. Optimum flow of material with varying characteristics is assured by adjustment of the output force of the drives. Further, drive isolation, independent hammer action, stress relieved construction, and few moving parts contribute to long, trouble-free service.
OperationThe car shakeout, suspended from a fixed location or traveling hoist, is lowered into position on the car top and operated intermittently. In accordance with the principle of natural frequency, a low amplitude, high frequency vibratory force produced by the motorized exciter assembly (first mass) is amplified through a rugged coil spring reactor system and transferred to twin impact hammers (second and third masses). These hammers then transmit a series of rapid, high energy vertical impacts directly into the car sides, loosening compacted, sluggish or frozen material and enhancing free-flow through the hopper bottoms.
FEATURES:
Two-Mass design draws less power; isolates drive system from hammer action.
Compact, self contained motorized counter-weight drives for totally sealed drive protection.
No belts, sheaves, guards or moving mechanical drive parts exposed to dirt, moisture or accidental damage.
Small, un-balanced force greatly reduces “coast-to-stop” time, eliminating cycle delays and need for plugging circuits.
Independent impact-hammer action provides more effective loosening force on material.
High frequency, low amplitude vibration reduces risk of frame fracture.