GK FLUIDBED PROCESSORS
Fluidization is the process of passing a fluid or gas through a distribution plate and then through a bed of material to suspend the material in a fluidized state. To achieve fluidization, the balance must be made to achieve the minimum fluidization velocity. At this velocity, drag force, along with buoyant force, counteracts the gravitational force, allowing the bed of solid materials to attain fluid-like properties.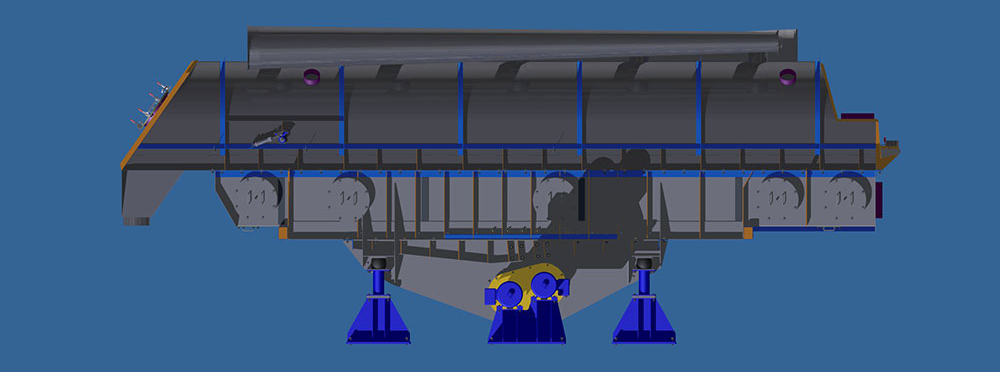
V2 VARIABLE VECTOR FLUID BED PROCESSORS
General Kinematics V2 Variable Vector Fluid Bed Processor drive brings material processing to the next level. The V2 Variable Vector technology allows you to quickly adjust product retention time to maximize contact of the process air stream. Easy to program controller allows single button adjustment, or can be tied into existing control systems for automated process control.
FEATURES:Easy to use control system allows adjustment of material retention time
Can be retrofitted to existing direct-drive processors to enhance existing operations
Monitors machine performance for precise control and speed adjustment
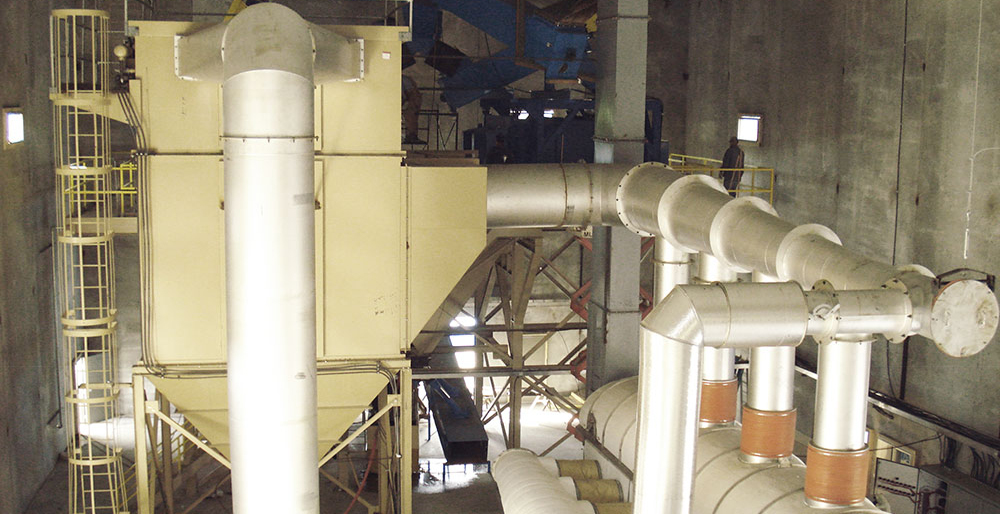
TWO-MASS VARIABLE ANGLE FLUID BEDS
General Kinematics Two-Mass Variable Angle Fluid Bed Dryers take a low energy, high throughput approach to variable angle conveyance and fluidization of materials. GK’s innovative V3 drive system with dual self-contained motorized drives, controls trough motion. Remote electrical or pneumatic control varies vibration angle from vertical to 45 degress, and amplitude from minimum to maximum at any material throw angle. These features combine to provide a precise means of adjusting retention time, flow rate and fluidized material bed depth during processing.
FEATURES:Application engineered with the stroke/frequency combination needed to minimize the matting of “tacky” materials.
Natural frequency design permits smooth starts and stops without isolation system resonance problems or the need for electrical motor braking.
Dependable operation with no belts, gears, or expensive bearings to maintain.
Bed depth regulated via manually or remotely controlled weirs and adjustable angle, allowing “zoning” of materials in process.
Available with complete custom engineered process air systems to suit your application requirements.
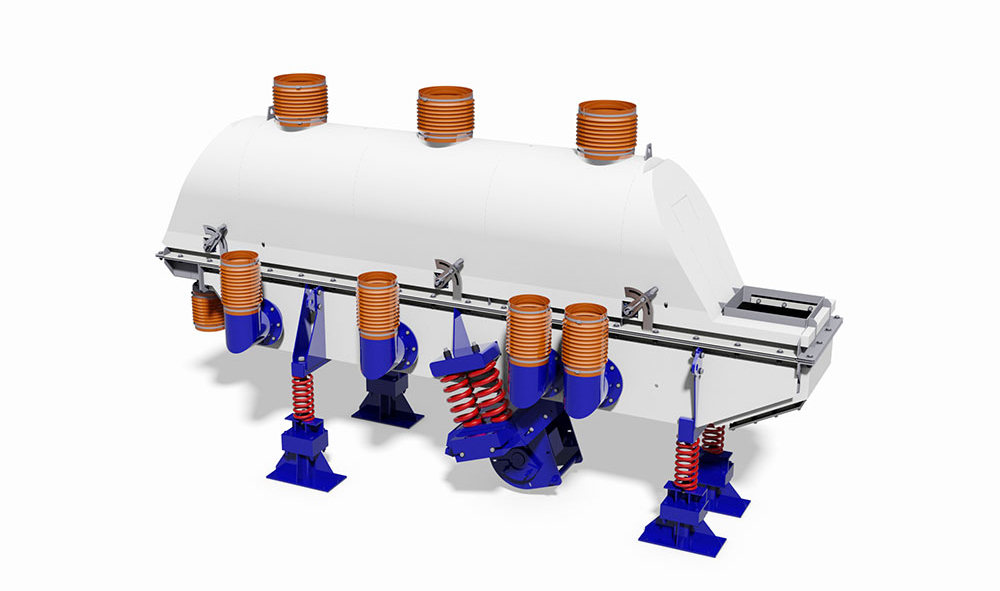
VIBRATING FLUID BED DRYER
Uniquely flexible for a wide range of continuous processing needs, GK’s vibrating fluid bed dryer for bulk processing is ideally used for heating, drying, cooling, coating, or elutriation. GK vibrating fluid beds are available in a variety of configurations and utilize vibratory agitation while passing a process gas through the material bed to suspend the material in a fluidized state. This increases available material surface area, allowing a faster and more complete processing of your material.
FEATURES:Each GK fluid bed dryer can heat, cool, dry, coat, and more, all in one unit.
Precision drilled, profile wire, exclusive T-P, and “fine hole sheet” distributor decks available to best meet your process needs.
Stainless steel, nickel alloy, and carbon steel construction available.
Optional drives with instantaneous adjustable stroke and angle of throw for special application requirements.
Adjustable weir assemblies for variable fluidized bed depth.
TEFC and TENV motor construction.
Soft vibration isolation springs facilitate above grade fluid bed installation.
Complete supply and exhaust air fluidized bed auxiliary packages for single source installations.
Fluid bed dryer units are custom designed to meet your specific throughput requirements.
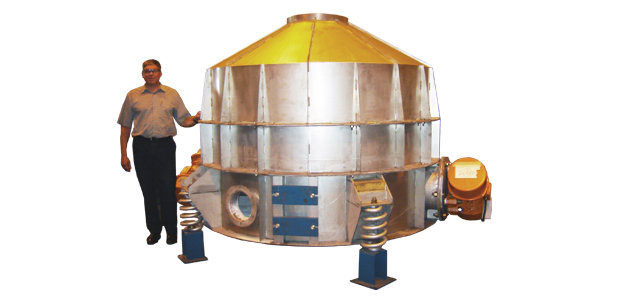
VIBRATORY ELUTRIATORS
General Kinematics Vibratory Elutriators combine vibration with air classification for separating materials of different densities. The collection efficiency of General Kinematics elutriators is maximized through the use of vibratory energy which stratifies the product and conveys it through the process. Once stratified, the lighter density material naturally rises to the top of the material stream and is ejected upwards into the exhaust hood of the machine.
GK vibratory elutriators can be configured in a straight conveyor-style fluid bed design or special spiral conveyor arrangements, depending on your process requirements. Contact General Kinematics for specific information regarding elutriation and other air classification technologies.
Separates materials of different densities using air and vibratory fluidization.
Custom engineered for your application.
Available in straight-line or spiral designs.
Complete air handling and process packages available.
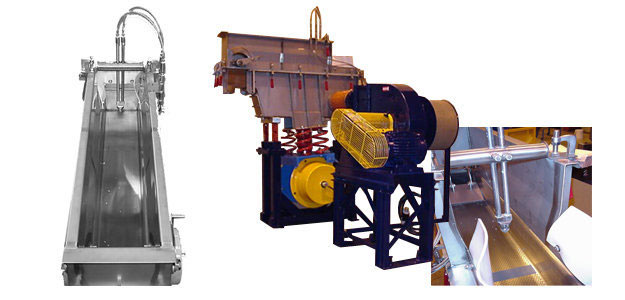
FLUID BED PROCESSOR ADDITIVE SPRAY COATING
The General Kinematics Additive Spray Coating works in conjunction with the General Kinematics Fluid Bed Processors. It provides superior dispersion of a wide range of additives in the chemical, food, and pharmaceutical industries. Typical applications include a broad category of granular solid and powder materials.
FEATURES:Atomizing nozzles with quick disconnect.
Excellent surface coverage.
Ideal for difficult applications with broad particle size distribution.
Two or more additives may be applied in series, followed by drying or cooling in a single unit.
Laboratory testing facilities available.
Custom design and fabrication for your specific process requirements.
Complete package including pumps and auxiliary equipment optional.
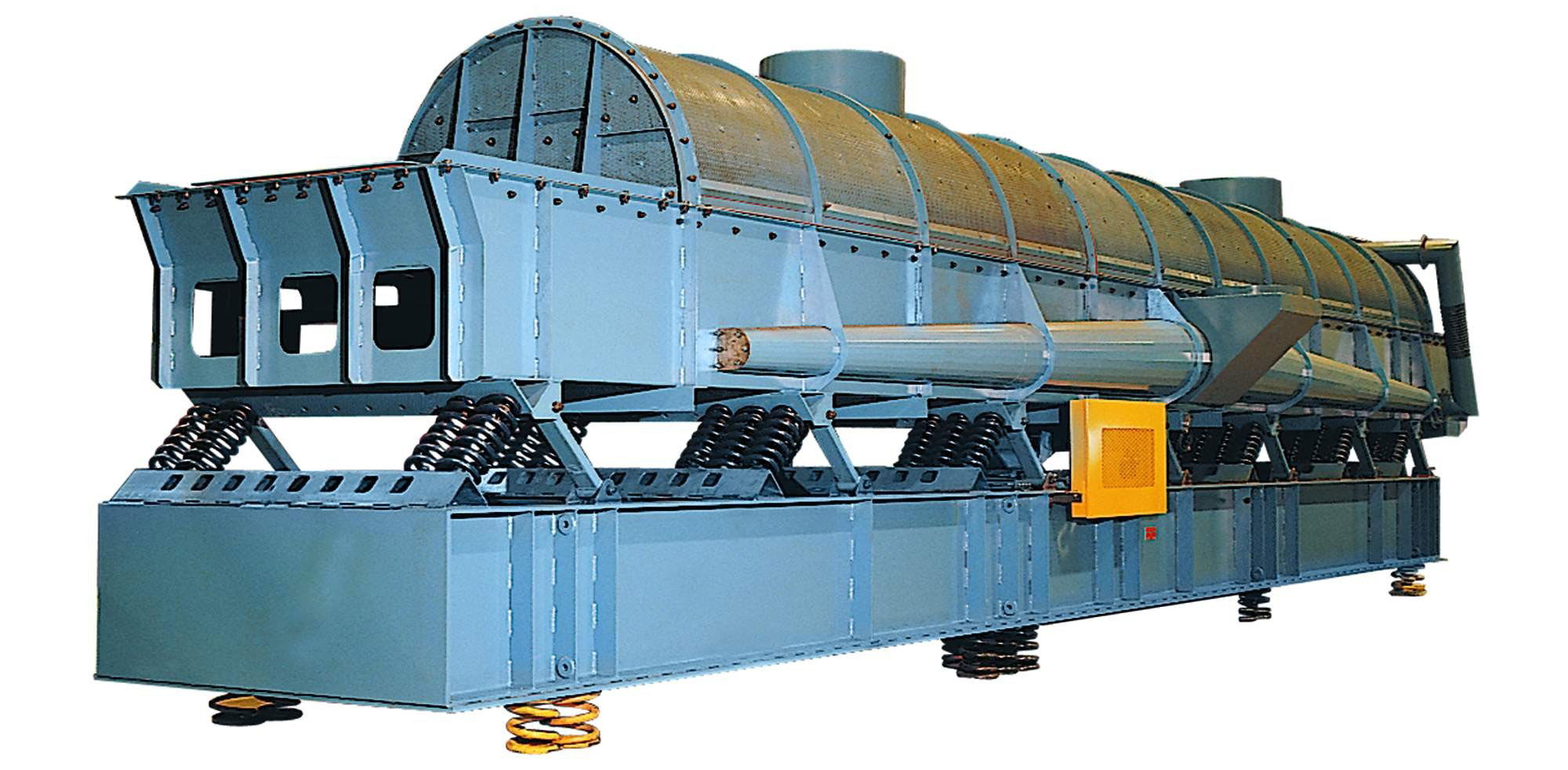
VIBRATORY FLUID BED SAND COOLERS
General Kinematics Vibratory Fluid Bed Sand Coolers are specially designed for evaporative cooling or drying of foundry sand. Air distribution decks are engineered to provide complete control of airflow for exceptional drying or cooling efficiency.
FEATURES:Choice of vibratory balancing styles or isolated designs to suit specific installation requirements for foundations or structures.
Custom designed to meet your sand cooling throughput needs to 500 tons or greater.
Infinitely adjustable controls provide variable retention time and improved process efficiency.
Inlet air distribution manifolds minimize costly stationary ductwork and supports.
High efficiency, low horsepower Two-Mass drive reduces energy requirements.