MUNICIPAL SOLID WASTE (MSW) SORTING SOLUTIONS
Municipal Solid Waste (MSW), more commonly known as your household trash, consists of packaging, and other items you dispose of at your curb every week. The challenge with processing MSW is the extreme physical characteristics associated with various commodities in the waste stream. Food scraps, newspapers and miscellaneous soft, flexible bagged material commingle with other contaminants like concrete, batteries, propane tanks, Christmas lights and chains that can damage traditional rotary equipment. GK’s proven technologies are the heart of MSW Sorting Systems around the world.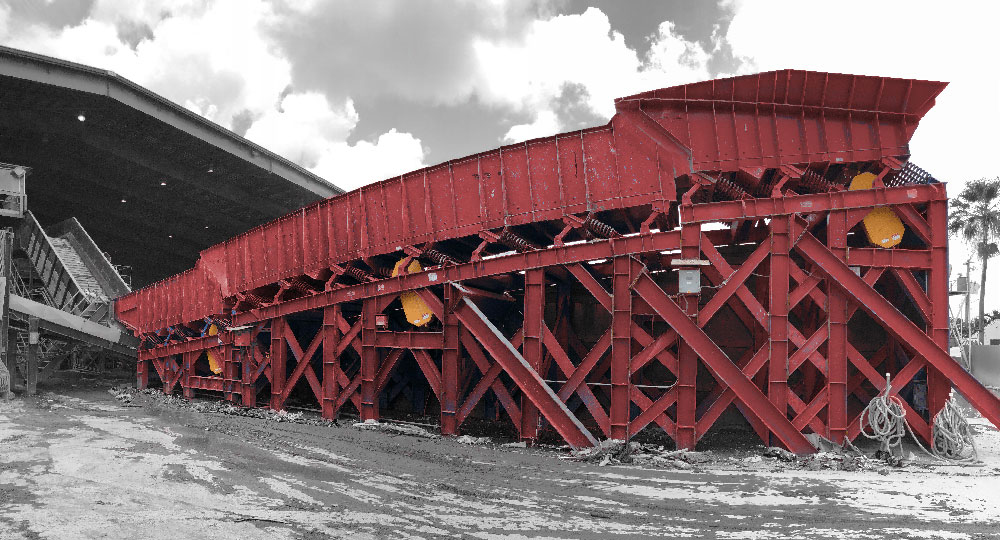
FINGER-SCREEN? 2.0 PRIMARY SCREEN
General Kinematics FINGER-SCREEN? Vibratory Separator for resource recycling has become an industry icon and proven in hundreds of applications around the world. Now, General Kinematics has raised the bar again. The new FINGER-SCREEN? 2.0 Primary Screen takes screening to the next level. Featuring all the benefits of the original, this new design in tandem arrangement, provides a longer displacement that moves traditionally difficult to screen materials.
Great for MSW, C&I and Single Stream applications, the superior performance of vibratory processing with GK’s unique FINGER-SCREEN? deck delivers highly efficient separation and classification. Like the FINGER-SCREEN? Primary Screen, FINGER-SCREEN? 2.0 features an enhanced vibratory action that spreads material across the deck for maximum utilization of the screen area. Tapered finger designs along with unique cam-out surfaces and staggered positions help to prevent material bypass. Separation performance is further improved as material freely cascades down the deck with less plugging, trapping, or pegging. The result: continuous, dynamic material flow to optimize separation and classification.
The FINGER-SCREEN? 2.0 boasts more energy, faster travel rate, and a higher lift for challenging materials including garbage bags, yard waste, and other lightweight, flexible materials. The longer displacement allows the unit to push through the elastic range of these materials more effectively. Unlike Rotary trommels, which aerate materials, cause blinding and pass long pokers with a high level of daily cleaning and maintenance requirements, FINGER-SCREEN? 2.0 separates materials based on 3D sizing with minimal blinding and minimal housekeeping. When used as the primary screen, FINGER-SCREEN? 2.0 provides the initial size separation which scalps off any potentially destructive contaminants, allowing the rest of the downstream equipment to operate effectively.
The FINGER-SCREEN? 2.0 Primary Screen is available in standard sizes with widths up to 96 inches (2400mm) with custom sizes engineered based on your application.
Vibratory motion evenly spreads material for maximum classification efficiency.
Longer displacement to screen traditionally difficult materials.
Staggered fingers prevent material bypass.
The width is unencumbered / open to process larger materials.
FINGER-SCREEN? 2.0 decks provide 3D sizing of product.
Cascading material flow helps separate entrapped items.
Unique cam-out surface helps eliminate catching and binding.
Tapered fingers gradually classify and free tangled materials.
Custom-engineered to meet your specific classification requirements.
Modular deck construction permits easy deck replacement.
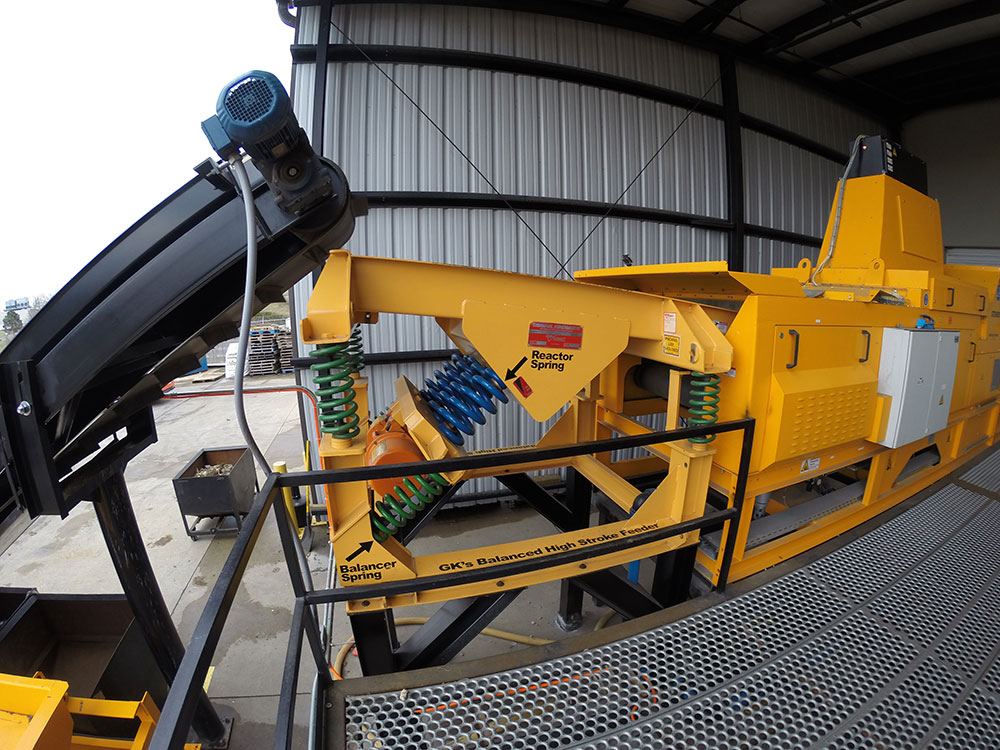
GK’S HIGH STROKE VIBRATING FEEDER
Cutting edge vibratory technology for enhanced material presentation
Challenged by our customers to do more within a limited footprint, General Kinematics developed the High Stroke Feeder (HSF) to create separation, improve on purity / recovery and increase the bottom line. GK’s HSF vibratory feeders improve on the presentation and recovery of various commodities by putting more energy into the material, thereby increasing separation of the various particles. In addition this spreads the materials across the width of the unit thereby resulting in enhanced material presentation for your optical sorter. General Kinematics has redefined the synergy between vibratory feeders and optical sorters.
High Stroke Creates Separation for Improved Purity
Faster Travel Speed = Better Material Separation = Optimal Recovery
More Energy Transmitted To the Material
Full Width Spread in Shorter Length
Lower Initial and Operating Costs
Dynamic Response to Negate Surge Loads
Up to 2/3 Less HP required to operate
OPTIONAL HSF FEATURES:
Specifically Engineered For the Industry
Optional Balanced Design Base
OEM Specific Models
Foot, Suspension or Combination Mounted Models
Mild Steel, Stainless Steel, Abrasion Resistant Steel Construction
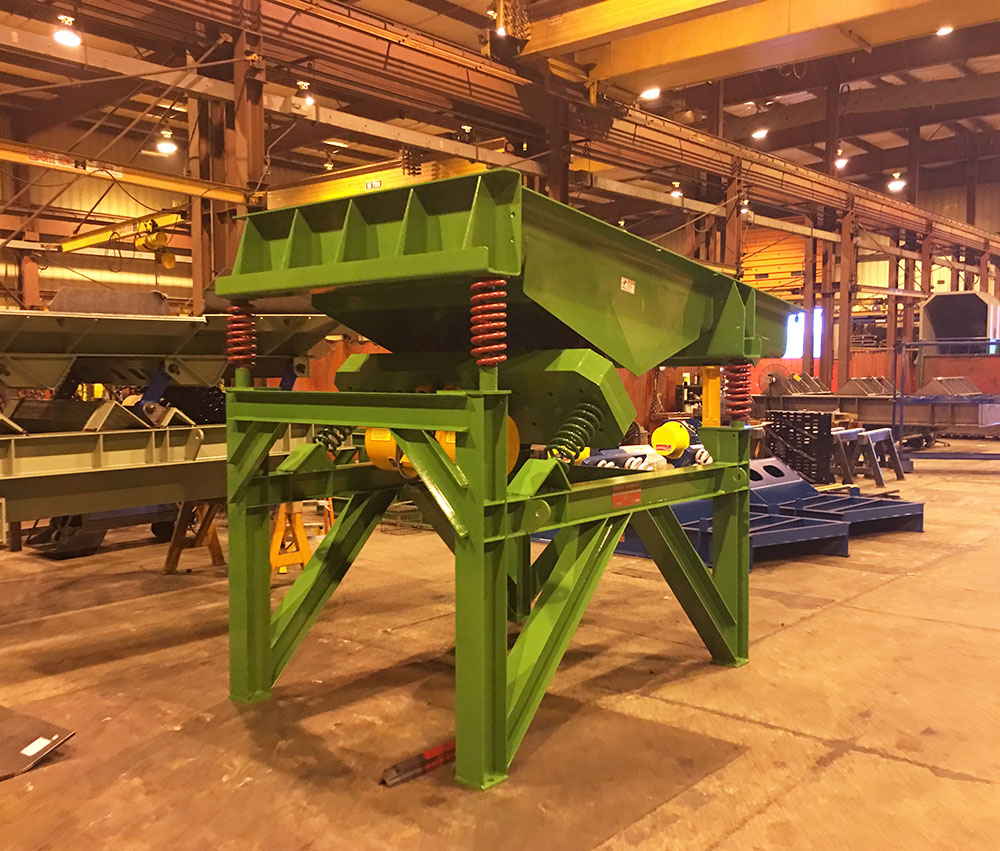
HD-HSF: HIGH DISPLACEMENT HIGH STROKE FEEDER
The latest vibratory technology for enhanced material presentation
Challenged again by our customers to do more within a limited footprint, General Kinematics has pushed the limits further and developed a High Displacement-High Stroke Feeder (HD-HSF) to create more separation, enhance purity levels, improve recovery and increase your bottom line. GK’s HD-HSF vibratory feeders improve the presentation of materials and recovery of various commodities by putting more energy into the material, thereby increasing separation of the various particles. In addition, this spreads the materials across the width of the unit thereby resulting in enhanced material presentation for your optical sorter. General Kinematics has redefined the synergy between vibratory feeders and optical sorters.
High Stroke Creates Separation for Improved Purity
Faster Travel Speed = Better Material Separation = Optimal Recovery
More Energy Transmitted To the Material
Full Width Spread in Shorter Length
Lower Initial and Operating Costs
Dynamic Response to Negate Surge Loads
Up to 2/3 Less HP required to operate
OPTIONAL HD-HSF FEATURES:
Specifically Engineered For the Industry
Optional Balanced Design Base which means no additional support structural work is required, thereby providing the best control, distribution and containment of materials
OEM Specific Models
Foot, Suspension or Combination Mounted Models
Mild Steel, Stainless Steel, Abrasion Resistant Steel Construction
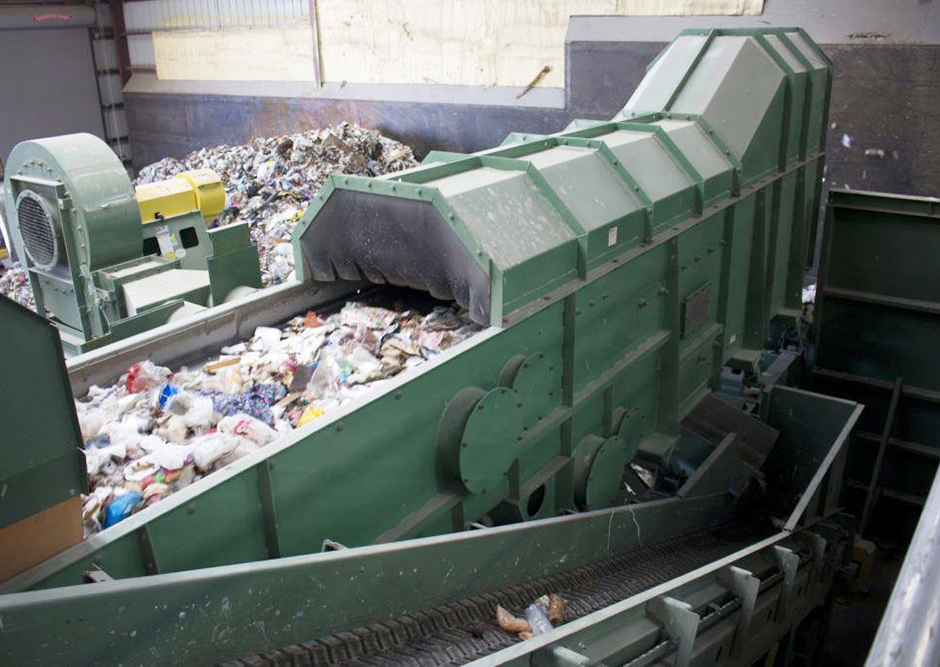
DE-STONER? AIR CLASSIFIERS FOR MSW
The General Kinematics DE-STONER? is a performance-proven method of separation and classification for a wide range of materials.
How the DE-STONER? works
Energy-efficient vibratory action and high velocity, low pressure air streams work in tandem to fluidize and stratify commingled materials according to differences in terminal particle velocity. Many DE-STONER? systems are designed with “air curtains” to provide further separation after the initial cut of “heavies”. The result: fast, efficient removal of heavy materials such as stones, metallics, and glass from lightweight materials such as aluminium, paper, plastics and wood.
Simple, dependable dry system
Our economical, completely dry DE-STONER? system eliminates the need for a water supply and other attendant “wet” system problems. However, the DE-STONER? can easily handle moist materials.
The DE-STONER? uses air instead of water to separate heavy product from light product, eliminating the mess and environmental hazards water separation creates.
Virtually jam-proof design with no moving separator parts.
Inherently simple, fully isolated design minimizes foundation requirements.
Versatile design separates material of different density, or equal densities with varying particle size.
DE-STONER? driven by energy efficient low horsepower motor.
Rugged, heavy duty construction withstands 24-hour operation
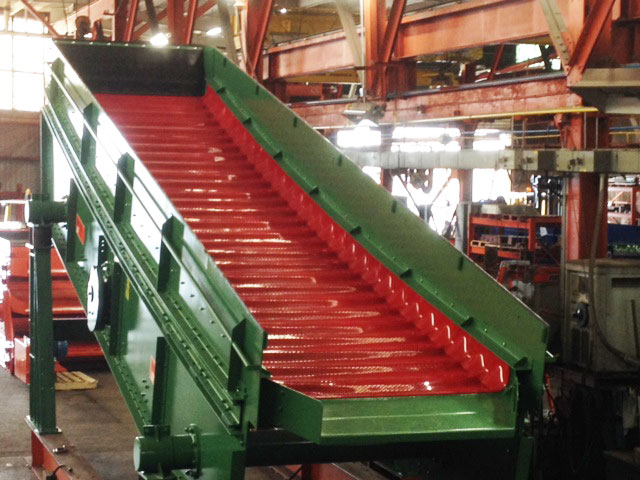
BIVI-TEC? FLEXIBLE MAT VIBRATORY SCREENS
There is a growing need to classify manufactured sand, sand and gravel, waste materials, raw materials, semi-finished products, and finished products more effectively. Conventional vibrating screens and trommel screens are very limited when screening materials that cause a build-up on the screen, which results in clogging or blinding of the screen openings.
Developed to screen even the most problematic materials, the bivi-TEC? offers a superior screening solution for Superpave sands, scrap materials, compost, incinerator ash and others. The bivi-TEC? ’s unique dual-vibratory screening process eliminates clogging and blinding of the screen openings to save downtime and increase productivity.
Dual vibration from a single drive is the unique feature of the bivi-TEC? Screen. Two weights, vibrating at the same frequency, move relative to each other which tensions and relaxes the screen mats. The linear momentum of both vibrating movements is adjustable, resulting in open screen surfaces and optimal screening performance.
To assure the most effective screening, high-acceleration forces must be transferred to the feed material. The bivi-TEC? Screen achieves these high forces by dynamically tensioning and relaxing the flexible screen mats using a dual-vibration principle. Enhanced by resonance, one drive can produce two vibration movements. The screen box is accelerated approximately 2g’s while the screen mats can receive up to 50g’s.
Applications, once judged impossible, can now be accomplished with the bivi-TEC? Screen.
THE BIVI-TEC? PROVES TO BE THE BEST MACHINE FOR SCREENING:
Manufactured sands, chips and aglime.
High-moisture materials combined with silt, mud, and clay.
Incinerator ash, trash, waste coal, clay, sand, and slag.
Compost, leafy materials, wood waste, and peat moss. Auto shredder fluff, and shredded tires.
Carpet, wallboard, scrap metal, and roofing shingles.
Fine screening of moist material.
Eliminates blinding and plugging.
Large effective screen area-high capacity.
Effective in all weather conditions.
Highly flexible for varying material requirements.
Long life polyurethane screen mats.
Rugged construction/low maintenance.
Lower energy usage.
Low profile.
Portable test unit available for on-site qualification.
General Kinematics offers bivi-TEC? in partnership with AEI, a licensee of Binder+Co AG.
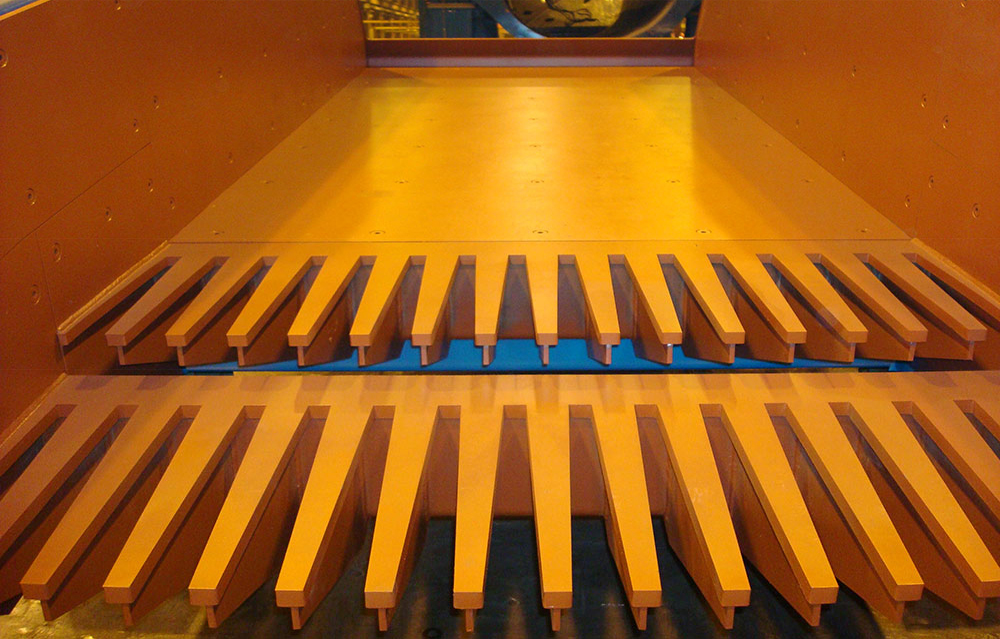
SECONDARY FINES SCREENS
General Kinematics’ High-Energy Secondary Screens in conjunction with GK’s FINGER-SCREEN? Primary Screen for resource recycling has proven to be highly successful in a wide range of applications that are prone to process challenges common to other types of screening media.
GK’s Secondary Screens use vibratory action to separate fines from the secondary sort line material. The Two-Mass, low horsepower design has few moving parts for minimal maintenance and maximum uptime. Secondary Screens are heavy-duty with superior wear resistance and durability compared to rotary trommels or star-type screens.
The heart of your sorting system
ncreased reliability, higher tonnage capacity and unsurpassed wear resistance make GK’s Secondary Screens the heart of sorting systems around the world. The superior performance of vibratory processing with GK’s unique FINGER-SCREEN? deck delivers highly efficient separation and classification. The vibratory action spreads material across the deck thereby lowering the bed depth for maximum utilization of the screen area. Tapered finger designs along with unique cam-out surfaces and staggered positions help to prevent material bypass. Separation performance is further enhanced as material freely cascades down the deck with less plugging, trapping, or pegging. The result: continuous, dynamic material flow to enhance and optimize separation and classification.
GK’s Secondary Screen is available in standard sizes with widths up to 72 inches (1800mm) with custom sizes engineered based on your application. Capable of processing high volume production rates up to 450 yards per hour (345 cubic meters per hour).
Vibratory motion evenly spreads material for maximum classification efficiency.
Staggered fingers prevent material bypass.
Cascading material flow helps separate entrapped items.
Unique cam-out surface helps eliminate catching and binding.
Tapered fingers gradually classify and free tangled materials.
Custom-engineered to meet your specific classification requirements.
Modular deck construction permits easy deck replacement.
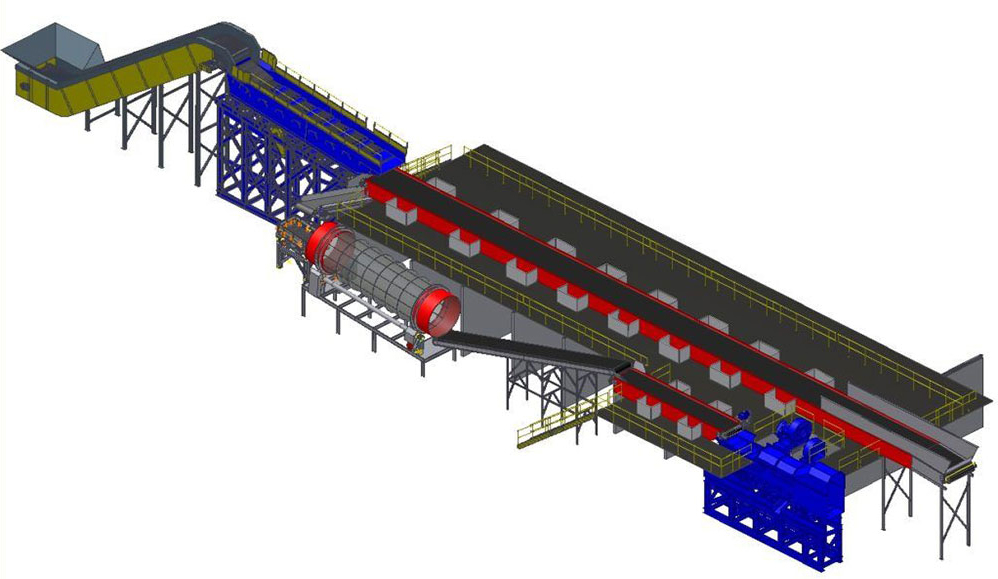
GK MSW / MRF SYSTEMS
General Kinematics MSW Systems maximize material recovery through the diversion of recoverable product for recycling, mass burn, or residual derived fuel (RDF). Combining proven methods of manual sorting with the proprietary operation of General Kinematics vibratory sorting technology, GK MSW Systems are unmatched in throughput and reliability.
The MINI-MRF? from General Kinematics is a low tonnage recycling system designed for high efficiency recovery of material. Base systems include primary screening with a quad station pick line, all mounted to an easy to install support system designed to utilize roll-off containers as material sorting bins. Additional options include extended pick lines, magnetic ferrous and non-ferrous separation, and GK’s DE-STONER? Air Classifiers to maximize your material recovery.
Turn-key, entry level (MINI-MRF?) or advanced system design.
Integration of General Kinematics’ SXS SCREEN? Vibrating Screener, DE-STONER? Air Classifier, and other technologies.
Mechanically separate material according to size and density.
Heavy-Duty pick belts and sorting bins.
Fully integrated control system.
Expandable systems as your business grows.
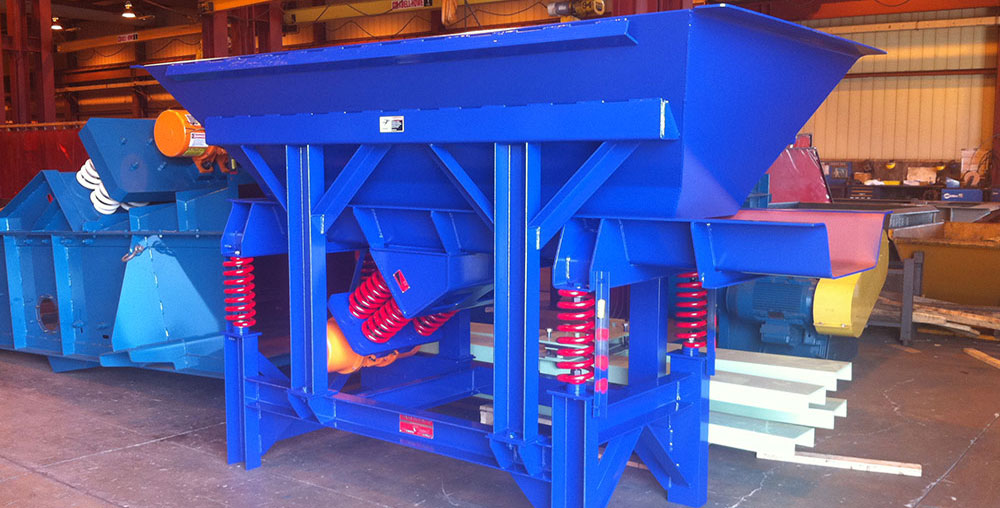
PARA-MOUNT II? VIBRATING FEEDERS
Proven performance and maintenance free operation make PARA-MOUNT II? Vibrating Feeders the first choice in vibratory feeders for the most demanding applications. PARA-MOUNT II? Vibrating Feeders in either fixed or Variable Force configurations utilize a sub-resonant Two-Mass system. Mass A (the exciter) energizes Mass B (the deck assembly) through precision engineered coil springs. Only small amounts of energy are needed to maintain the natural energy stored and released by the spring system. What this means for you is dynamic response to load surges, increased feed capacity, and exceptional reliability and ease of maintainability. PARA-MOUNT II? Vibrating Feeders are specifically designed to enhance your process.
FEATURES:Low maintenance, maximum uptime for reliable performance.
Simple, extra-heavy duty construction for years of trouble free service.
Two-Mass, sub-resonant natural frequency design is dynamically responsive to automatically maintain constant feed rate for varying load and material changes.
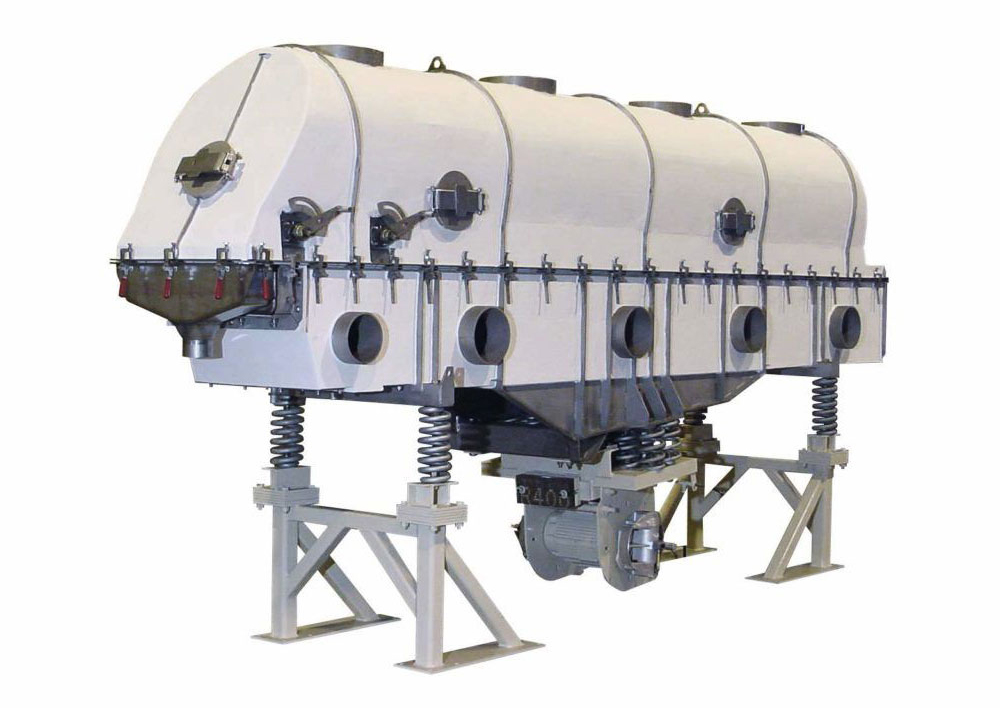
FLUIDBED DRYERS FOR MUNICIPAL SOLID WASTE (MSW) AND REFUSE DERIVED FUEL (RDF)
General Kinematics Vibratory Fluid Bed Dryers are unmatched in bulk processing performance. Each Fluid Bed Dryer is custom engineered to match your specific process needs based on: temperature limitations, moisture requirements, and volatile organic compound (VOC) emissions. Custom engineered with a variety of options makes GK Fluid Bed Dryers a versatile part of your process operations.
Capable of continuous or batch processing, GK Fluid Bed Dryers are designed to dry at low temperatures to eliminate melting, charring or burning materials, thereby reducing fire hazards associated with traditional drying techniques. GK Fluid Bed Dryers utilize vibratory agitation while passing a process gas through the material bed to suspend the material in a fluidized state. This increases available material surface area, allowing a faster and more complete processing of your material.
Contact GK for the complete drying package to increase your throughput while enhancing your product quality.
GK Vibratory Fluid Bed Dryers are capable of drying at low temperatures.
Reduce fire hazards associated with traditional drying techniques.
Engineered in optimal sizes to maximize your process throughput.
Fluidized beds can cool, dry, heat, and more.
Stainless steel, nickel alloy, and carbon steel construction available.
Adjustable weir assemblies for variable fluidized bed depth.
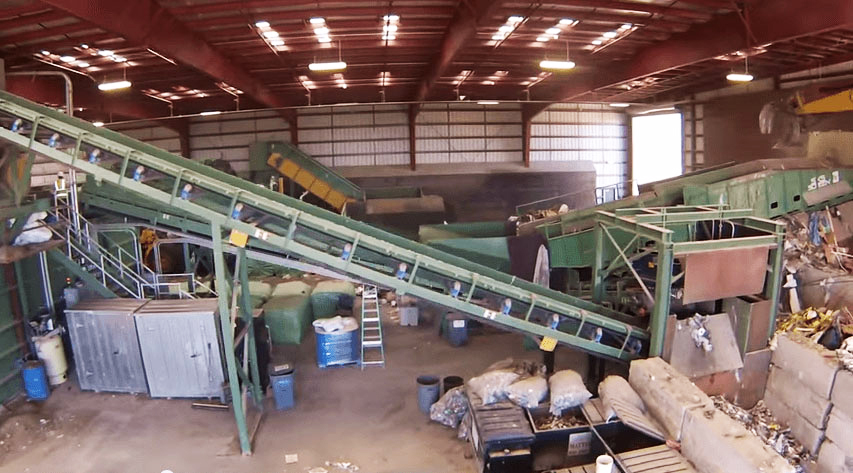
MULTI-STREAM? RECYCLING SYSTEMS
Capable of processing C&D, MSW or ICI all on one system, the MULTI-STREAM? Recycling System gives you the flexibility to process different types of material as your incoming waste stream changes. Pre-sorting on the ground is eliminated by incorporating General Kinematics’ primary screening technology to process any off spec contaminates in the waste stream. The MULTI-STREAM? Recycling System is custom engineered and durable enough to handle any material you throw at it.
FEATURES:Turn-key, entry level or advanced system design.
Integration of General Kinematics’ SXS SCREEN? Vibrating Screener, DE-STONER? Air Classifier, and other technologies for effective separation of commodities.
Mechanically separate material according to size and density.
Heavy-Duty pick belts and sorting bins.
Fully integrated control system.
Expandable systems as your business grows.