SINGLE-STREAM / C&I RECYCLING EQUIPMENT
Single stream or C&I Recycling refers to a process in which all recyclables are mixed together in a collection truck, instead of being sorted by material type (i.e. newspaper, plastic, glass, aluminum, etc.) by the resident. General Kinematics vibratory equipment is the heart of systems to manage these recyclables around the world. Engineered and manufactured to your process and application, these units are renowned for their ability to convey, screen, and separate your waste stream to produce the cleanest commodities possible.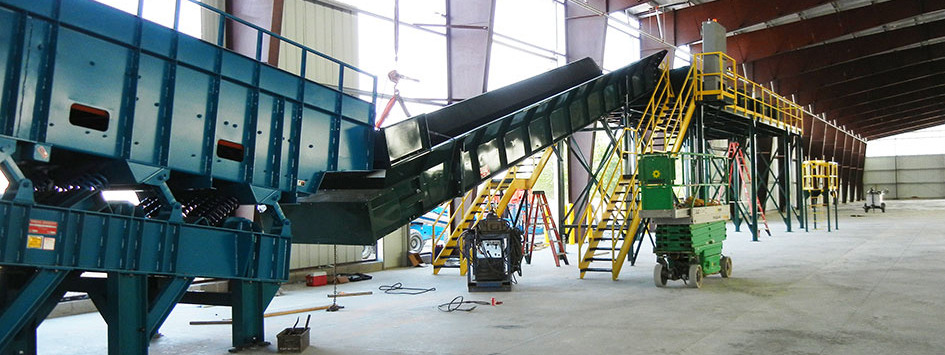
FINGER-SCREEN? PRIMARY VIBRATORY SCREEN
General Kinematics patented FINGER-SCREEN? Primary Screen design concept for resource recycling has proven to be highly successful in a wide range of applications that are prone to process challenges common to other types of screening media.
The heart of your sorting system
The superior performance of vibratory processing with GK’s unique FINGER-SCREEN? deck delivers highly efficient separation and classification. The vibratory action spreads material across the deck thereby lowering the bed depth for maximum utilization of the screen area. Tapered finger designs along with unique cam-out surfaces and staggered positions help to prevent material bypass. Separation performance is further enhanced as material freely cascades down the deck with less plugging, trapping, or pegging. The result: continuous, dynamic material flow to enhance and optimize separation and classification.
The FINGER-SCREEN? Primary Screen is available in standard sizes with widths up to 72 inches (1800mm) with custom sizes engineered based on your application. This vibratory screener is capable of processing high volume production rates up to 750 yards per hour (600 cubic meters per hour).
Vibratory motion evenly spreads material for maximum classification efficiency.
Staggered fingers prevent material bypass.
Cascading material flow helps separate entrapped items.
Unique cam-out surface helps eliminate catching and binding.
Tapered fingers gradually classify and free tangled materials.
Custom-engineered to meet your specific classification requirements.
Modular deck construction permits easy deck replacement.
PhotosVideosCase StudiesAdditional InfoContact
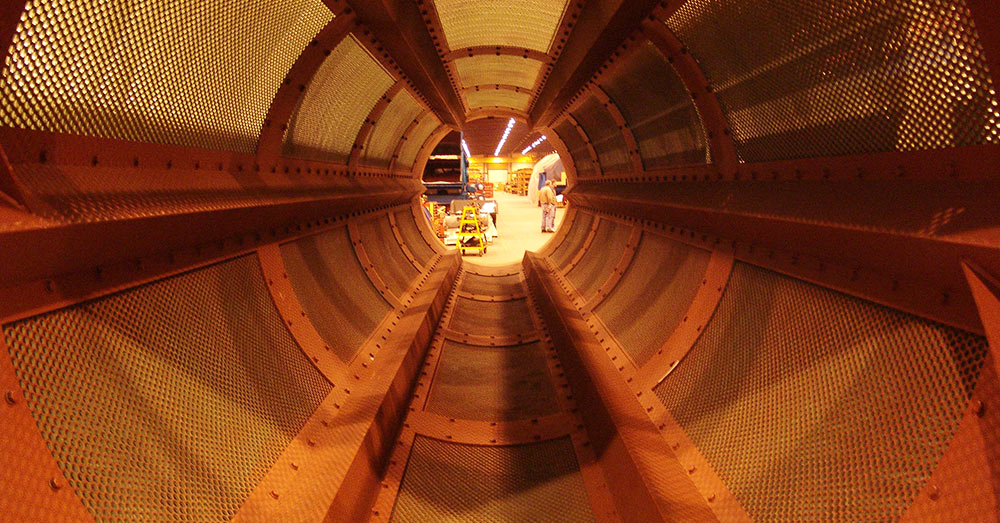
ROTARY TROMMEL
GK Rotary Trommels are designed to efficiently separate and size recyclable material that is prone to sticking or jamming in other secondary separation technology. Heavy-duty drive systems and trommel bodies are easy to clean and easy to maintain. Super-duty trommel designs impart greater impact force to the product and are optimized for materials such as glass recovery and shingle processing. For more information on rotary trommels, contact a GK Recycling Technology expert.
FEATURES:Material infeed can be through either a bag opener for municipal waste or to a bypass feeder for C&D and other non-bagged materials.
Separation is achieved using GK’s FINGER-SCREEN? for initial separation, a vibratory fines screen, and through the use of GK’s DE-STONER? Air Classifier.
Ferrous separation is also available on the A line, B line, or both.
Find out why recycling professionals around the world are choosing the FINGER-SCREEN? 2.0 to replace trommels to reduce blinding and downtime!
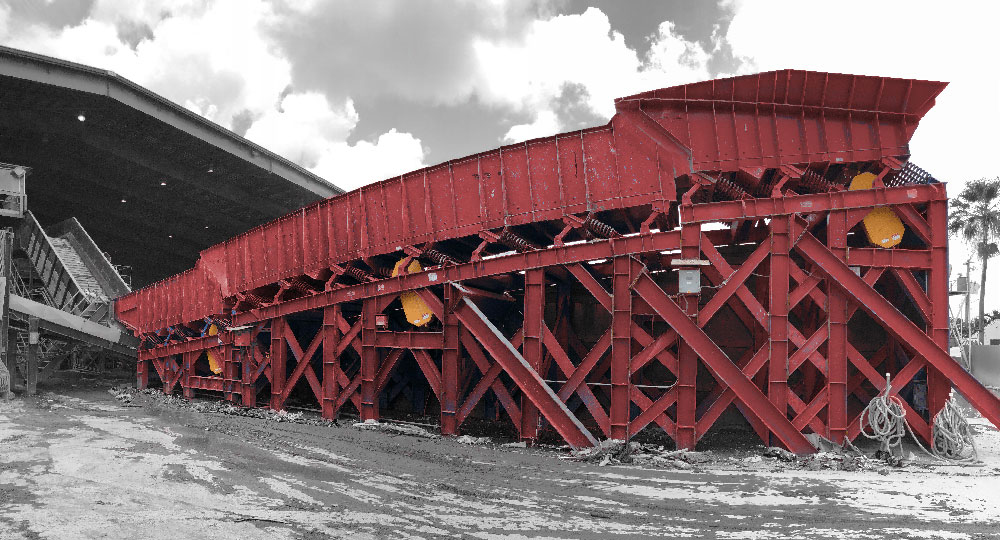
FINGER-SCREEN? 2.0 PRIMARY SCREEN
General Kinematics FINGER-SCREEN? Vibratory Separator for resource recycling has become an industry icon and proven in hundreds of applications around the world. Now, General Kinematics has raised the bar again. The new FINGER-SCREEN? 2.0 Primary Screen takes screening to the next level. Featuring all the benefits of the original, this new design in tandem arrangement, provides a longer displacement that moves traditionally difficult to screen materials.
Great for MSW, C&I and Single Stream applications, the superior performance of vibratory processing with GK’s unique FINGER-SCREEN? deck delivers highly efficient separation and classification. Like the FINGER-SCREEN? Primary Screen, FINGER-SCREEN? 2.0 features an enhanced vibratory action that spreads material across the deck for maximum utilization of the screen area. Tapered finger designs along with unique cam-out surfaces and staggered positions help to prevent material bypass. Separation performance is further improved as material freely cascades down the deck with less plugging, trapping, or pegging. The result: continuous, dynamic material flow to optimize separation and classification.
The FINGER-SCREEN? 2.0 boasts more energy, faster travel rate, and a higher lift for challenging materials including garbage bags, yard waste, and other lightweight, flexible materials. The longer displacement allows the unit to push through the elastic range of these materials more effectively. Unlike Rotary trommels, which aerate materials, cause blinding and pass long pokers with a high level of daily cleaning and maintenance requirements, FINGER-SCREEN? 2.0 separates materials based on 3D sizing with minimal blinding and minimal housekeeping. When used as the primary screen, FINGER-SCREEN? 2.0 provides the initial size separation which scalps off any potentially destructive contaminants, allowing the rest of the downstream equipment to operate effectively.
The FINGER-SCREEN? 2.0 Primary Screen is available in standard sizes with widths up to 96 inches (2400mm) with custom sizes engineered based on your application.
Vibratory motion evenly spreads material for maximum classification efficiency.
Longer displacement to screen traditionally difficult materials.
Staggered fingers prevent material bypass.
The width is unencumbered / open to process larger materials.
FINGER-SCREEN? 2.0 decks provide 3D sizing of product.
Cascading material flow helps separate entrapped items.
Unique cam-out surface helps eliminate catching and binding.
Tapered fingers gradually classify and free tangled materials.
Custom-engineered to meet your specific classification requirements.
Modular deck construction permits easy deck replacement.
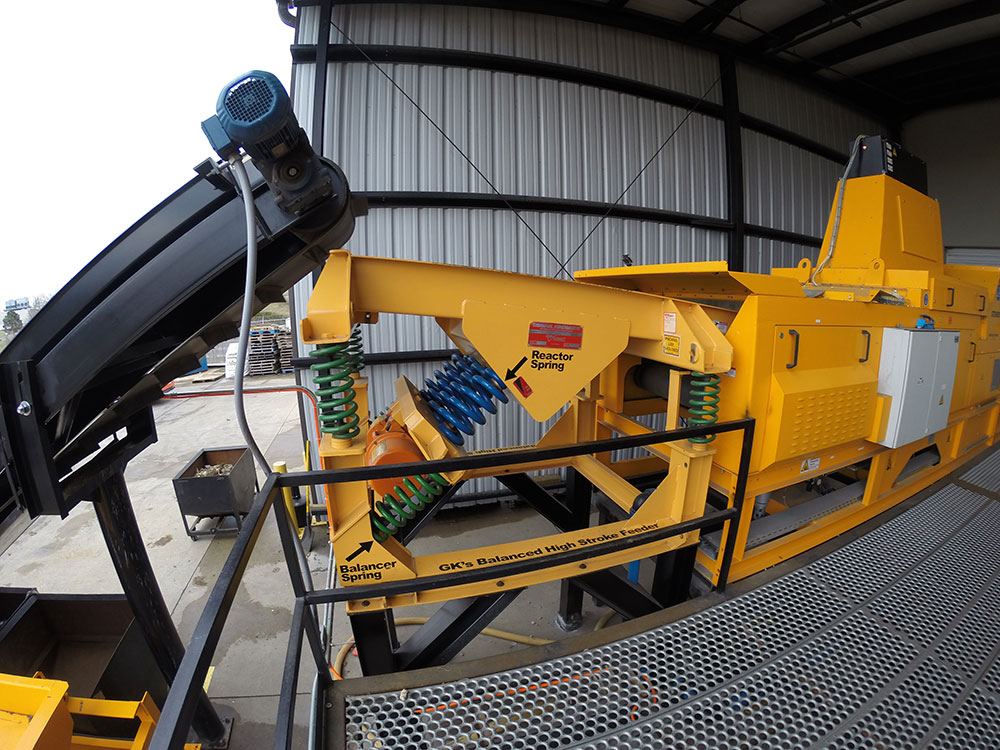
GK’S HIGH STROKE VIBRATING FEEDER
Cutting edge vibratory technology for enhanced material presentation
Challenged by our customers to do more within a limited footprint, General Kinematics developed the High Stroke Feeder (HSF) to create separation, improve on purity / recovery and increase the bottom line. GK’s HSF vibratory feeders improve on the presentation and recovery of various commodities by putting more energy into the material, thereby increasing separation of the various particles. In addition this spreads the materials across the width of the unit thereby resulting in enhanced material presentation for your optical sorter. General Kinematics has redefined the synergy between vibratory feeders and optical sorters.
High Stroke Creates Separation for Improved Purity
Faster Travel Speed = Better Material Separation = Optimal Recovery
More Energy Transmitted To the Material
Full Width Spread in Shorter Length
Lower Initial and Operating Costs
Dynamic Response to Negate Surge Loads
Up to 2/3 Less HP required to operate
OPTIONAL HSF FEATURES:
Specifically Engineered For the Industry
Optional Balanced Design Base
OEM Specific Models
Foot, Suspension or Combination Mounted Models
Mild Steel, Stainless Steel, Abrasion Resistant Steel Construction
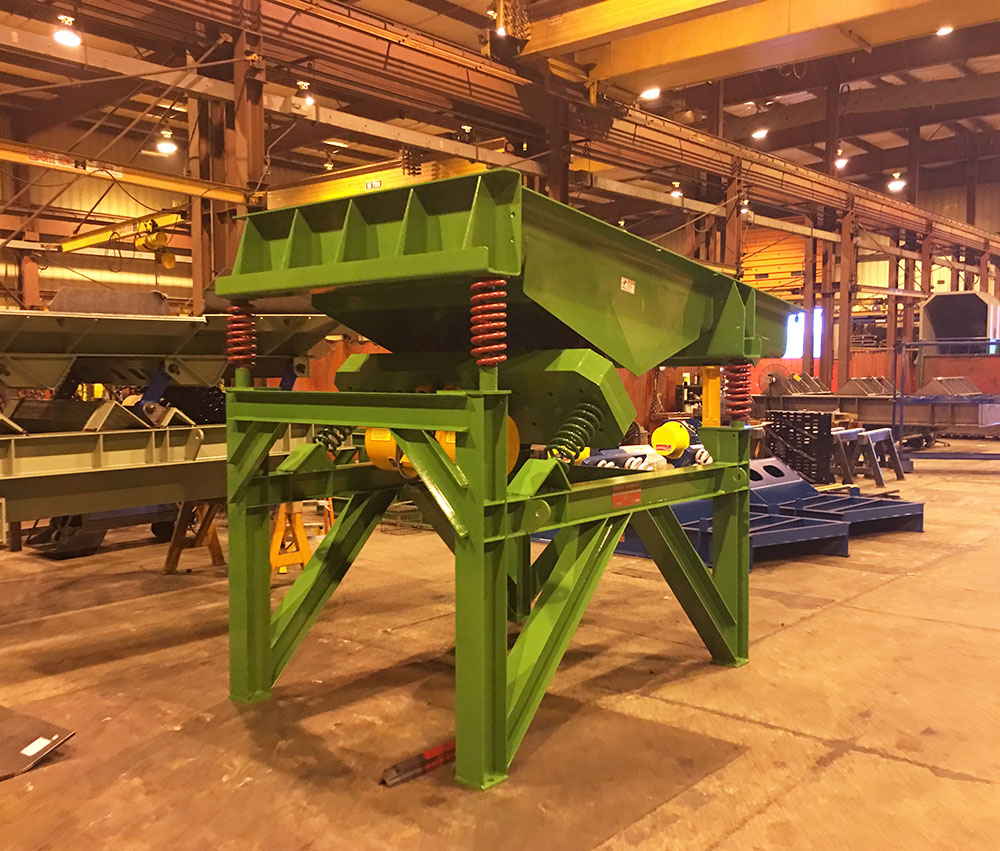
HD-HSF: HIGH DISPLACEMENT HIGH STROKE FEEDER
The latest vibratory technology for enhanced material presentation
Challenged again by our customers to do more within a limited footprint, General Kinematics has pushed the limits further and developed a High Displacement-High Stroke Feeder (HD-HSF) to create more separation, enhance purity levels, improve recovery and increase your bottom line. GK’s HD-HSF vibratory feeders improve the presentation of materials and recovery of various commodities by putting more energy into the material, thereby increasing separation of the various particles. In addition, this spreads the materials across the width of the unit thereby resulting in enhanced material presentation for your optical sorter. General Kinematics has redefined the synergy between vibratory feeders and optical sorters.
High Stroke Creates Separation for Improved Purity
Faster Travel Speed = Better Material Separation = Optimal Recovery
More Energy Transmitted To the Material
Full Width Spread in Shorter Length
Lower Initial and Operating Costs
Dynamic Response to Negate Surge Loads
Up to 2/3 Less HP required to operate
OPTIONAL HD-HSF FEATURES:
Specifically Engineered For the Industry
Optional Balanced Design Base which means no additional support structural work is required, thereby providing the best control, distribution and containment of materials
OEM Specific Models
Foot, Suspension or Combination Mounted Models
Mild Steel, Stainless Steel, Abrasion Resistant Steel Construction

GK ROD DECK SCREEN FOR SINGLE STREAM
General Kinematics Rod Deck Screen for Single Stream is specifically designed for the separation of difficult material that is prone to sticking or blinding in traditional screening applications. The secret behind the rod decks ability to perform lies in the flexibility and increase screen area of the rod decks within the deck section, while maintaining the designed screening tolerance. With more open area, less blinding, less hang ups, the heavy-duty design of GK Rod Deck Screens allow for abrasive, heavy, wet, or otherwise difficult material to easily screen.
The high-stroke capabilities of the GK’s vibratory screening equipment combined with the flexibility of the engineered rod deck assemblies, creates a versatile and high performance screening solution to maximize sorting in your process application.
Separates material that blinds on traditional screening surfaces.
GK Rod Decks allow for abrasive, heavy, wet, or otherwise difficult material to easily screen.
Increased screening area.
Easy to clean and maintain.
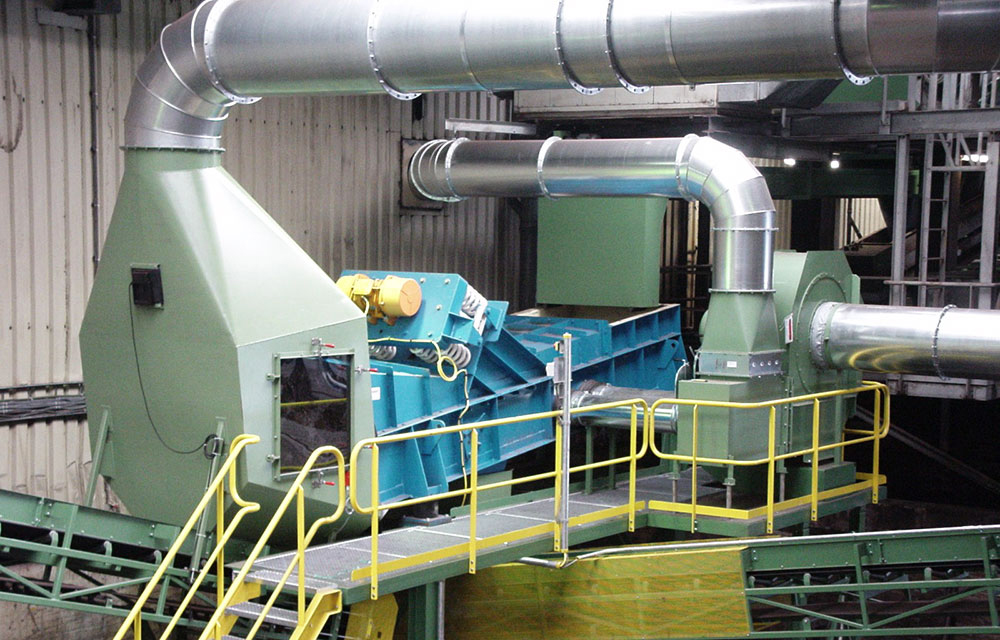
SINGLE KNIFE DE-STONER? AIR CLASSIFIER
The GK Single Knife DE-STONER? Air Classifier is a fully proven design operating efficiently in various separating applications. This dry classifying system is capable of handling continuous, high volume production.
The completely dry system eliminates water handling and other “wet” system problems, yet can easily handle moist materials. The DE-STONER? Air Classifier combines vibration, fluidization with a high velocity / low pressure air stream to stratify material. Differences in terminal velocity of particles result in heavy items such as glass, metallics, and stones to be removed from lighter items such as paper, plastic and small wood.
The heart of your sorting system
1. Vibratory action moves material, with high density material settling to the bottom of the trough.
2. Fines drop out section (optional) removes smaller particle sizes like broken glass or dirt before reaching air fluidizer.
3. Air fluidizing section blows air through the material and creates turbulence to promote material stratification.
4. Material conveys over the air knife into the air stream. Heavier materials falls through the air stream to the discharge chute.
5. Marginal density material falls on the adjustable landing plate and drops back into discharge chute.
6. Lights materials are carried beyond the landing plate and convey to the end of the DE-STONER?.
7. Ultra light materials like thin film or paper are carried in the air stream to the product discharge zone.
Optional add-on’s include GK’s
Fluff Knife Upgrade or DE-STONER? Drop-Out Boxes.
SUCCESSFUL SEPARATING AND CLASSIFYING APPLICATIONS INCLUDE:
C&D materials
RDF fuel
Glass
Commingled materials
Shredded MSW
Shredded auto scrap fluff
Bio-mass fuel
The DE-STONER? Air Classifier uses air to separate heavy product from light product.
Environmental hazards associated with water separation is thus eliminated along with the inherent mess.
Easily adjustable to obtain varying degrees of separation.
Adaptable to a wide variety of products.
Separates material of different density, or of same density with different particle size.
Virtually jam-proof. No moving parts in contact with material flow.
Low energy demand with low HP motor and GK’s proven Two-Mass design.
Fully isolated design minimizes foundation requirements.
Heavy-duty, built to last construction.
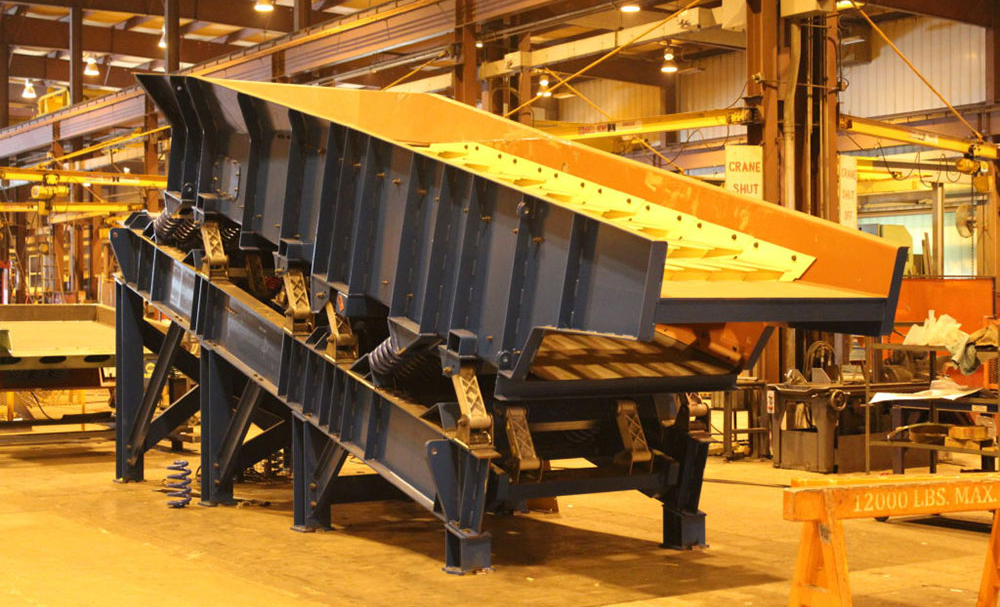
VIBRATORY OCC SCREEN
The SXS SCREEN? for OCC can be used to separate OCC in addition to the withstanding contaminated material streams. The higher stroke translates to faster travel rates and more energy into the product to provide better separation and screening. Able to handle concrete, chains and other challenging materials without hesitation, the vibratory SXS SCREEN? resolves the persistent and costly problems experienced with rotary OCC screens and star screens. The vibratory motion provides size separation without fluffing the material. Available in custom widths and lengths to best fit your throughput and application these screens are a great alternative to star screens and disc screens. The SXS SCREEN? for OCC is easier and safer to work on in terms of maintenance, cleaning and accessibility.
SXS SCREEN? FOR OCCRugged design, capable of processing contaminated waste streams.
Low head room requirements for installation.
Custom widths to meet your specific separation requirements.
Dependable, energy-saving, natural frequency vibratory drive.
Provides size separation without fluffing paper.
Less material hang up. Easy deck access.
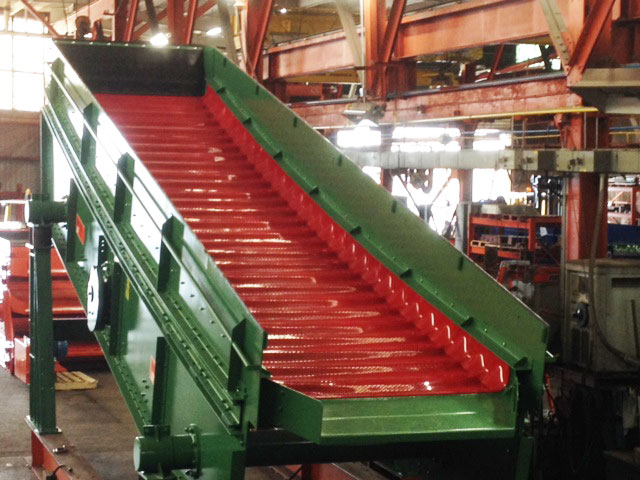
BIVI-TEC? FLEXIBLE MAT VIBRATORY SCREENS
There is a growing need to classify manufactured sand, sand and gravel, waste materials, raw materials, semi-finished products, and finished products more effectively. Conventional vibrating screens and trommel screens are very limited when screening materials that cause a build-up on the screen, which results in clogging or blinding of the screen openings.
Developed to screen even the most problematic materials, the bivi-TEC? offers a superior screening solution for Superpave sands, scrap materials, compost, incinerator ash and others. The bivi-TEC? ’s unique dual-vibratory screening process eliminates clogging and blinding of the screen openings to save downtime and increase productivity.
Dual vibration from a single drive is the unique feature of the bivi-TEC? Screen. Two weights, vibrating at the same frequency, move relative to each other which tensions and relaxes the screen mats. The linear momentum of both vibrating movements is adjustable, resulting in open screen surfaces and optimal screening performance.
To assure the most effective screening, high-acceleration forces must be transferred to the feed material. The bivi-TEC? Screen achieves these high forces by dynamically tensioning and relaxing the flexible screen mats using a dual-vibration principle. Enhanced by resonance, one drive can produce two vibration movements. The screen box is accelerated approximately 2g’s while the screen mats can receive up to 50g’s.
Applications, once judged impossible, can now be accomplished with the bivi-TEC? Screen.
THE BIVI-TEC? PROVES TO BE THE BEST MACHINE FOR SCREENING:
Manufactured sands, chips and aglime.
High-moisture materials combined with silt, mud, and clay.
Incinerator ash, trash, waste coal, clay, sand, and slag.
Compost, leafy materials, wood waste, and peat moss. Auto shredder fluff, and shredded tires.
Carpet, wallboard, scrap metal, and roofing shingles.
Fine screening of moist material.
Eliminates blinding and plugging.
Large effective screen area-high capacity.
Effective in all weather conditions.
Highly flexible for varying material requirements.
Long life polyurethane screen mats.
Rugged construction/low maintenance.
Lower energy usage.
Low profile.
Portable test unit available for on-site qualification.
General Kinematics offers bivi-TEC? in partnership with AEI, a licensee of Binder+Co AG.