SAND ATTRITION
Effective sand attrition improves production rates and reduces costs for material handling and new sand. GK mills reduce sand lumps to grain size and remove tramp metal while shakeouts and drums classify, separate, crush, and screen sand in one efficient system.GK’s vibratory and rotary equipment is heavy duty, low maintenance with minimum downtime.
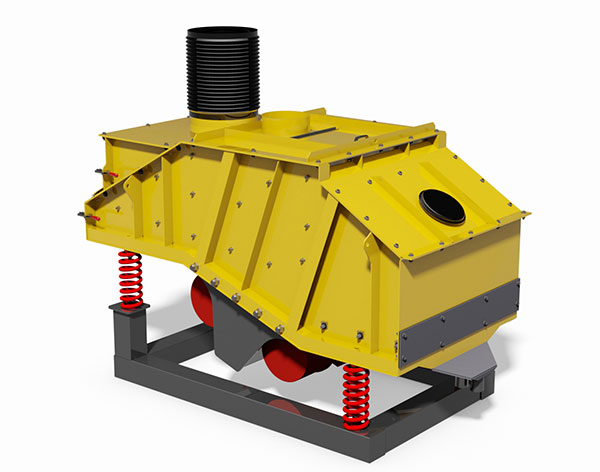
VIBRA-MILL? VIBRATORY BATCH SAND RECLAMATION
SHAKES, AGITATES, VIBRATES, TUMBLES, AND ABRADES UP TO 4 FOOT LUMPS TO MINUS 20 MESH GRAIN SIZE. AUTOMATICALLY.
The VIBRA-MILL? Vibratory Batch Sand Reclamation has proven itself in scores of foundries as both a total attrition mill and as a sand preconditioner. It often eliminates the need for larger, more costly equipment and systems while actually improving production rates. Also, the VIBRA-MILL? sand reclamation efficiency greatly reduces the purchase of new sand.
CONSTRUCTION
Mounted on low-stress steel coil isolation springs to minimize floor vibration, VIBRA-MILL? features an open tub design that eliminates maintenance and operational problems inherent in multiple deck units. With GK’s standard VIBRA-MILL? design, manual clean-out of the tub is unnecessary. GK now offers optional enclosed VIBRA-MILL designs to reduce dust and airborne silica.
Compact in design, the largest VIBRA-MILL? model occupies just under 81 square feet of floor space. It can easily be incorporated into most existing systems for improved production and savings.
CAPACITY
Production rates of up to fifty+ tons per hour can be sustained while reducing a normal mixture of lumps and sand to original grain size.
FINAL GRAIN SIZE
Lumps are reduced to minus 20 mesh with original grain size distribution and corresponding reduction in L.O.I. With proper addition of new sand, reclaimed material is clean and ready for new mold production without further attrition.
SEPARATION CAPABILITY
To assure clean sand, tramp material such as metallics, ceramics, core wires, etc. are conveyed and unloaded through an air operated gate at one end of the unit.
At the opposite end, fine sand passes through an air sweep exhaust where fine organics are removed; then also over a final sizing screen for separation of ceramic and metallic particles.
LOW NOISE LEVEL
Quiet, smooth operating VIBRA-MILL? conforms to the most stringent industry noise specifications.
DRIVE SYSTEM
Drive system is a tandem unit of self-contained motorized drives from 2 to 7 ? hp. each, depending on the VIBRA-MILL? model. They create the vibrating action necessary to process sand lumps into original grain size. Motors are specially constructed for vibratory service, and feature dust-tight, totally enclosed design. Drives are easily accessible for service and maintenance.
On standard VIBRA-MILL? models, a third drive is used during the trash unloading cycle to produce a reverse conveying action and to clear the primary screen. For High-Energy VIBRA-MILL? designs, clean out must be completed manually.
Motor dependability, simplified drive, and easy accessibility contribute to the trouble-free performance of VIBRA-MILL? equipment.
NOT JUST FOR SAND
VIBRA-MILL? is a truly versatile piece of equipment. In fact, there are many industries where VIBRA-MILL? tumbling and attrition action can be added to the processing cycle, to speed up production and save costs. For example, the scrap metal industry uses VIBRA-MILL? to process metal pieces before briquetting. Foundries also use VIBRA-MILL? for recovery of non-ferrous materials, like aluminum, bronze, brass, and special alloys.
Contact your General Kinematics representative about how GK’s VIBRA-MILL? can help your operation achieve greater production savings.
Special vibratory service motors for increased uptime.
Various feed options depending on application.
High capacity reclamation rates.
Simple, open tub design for easy loading.
Optional totally enclosed designs available.
Single jam-proof deck.
Provides fines removal.
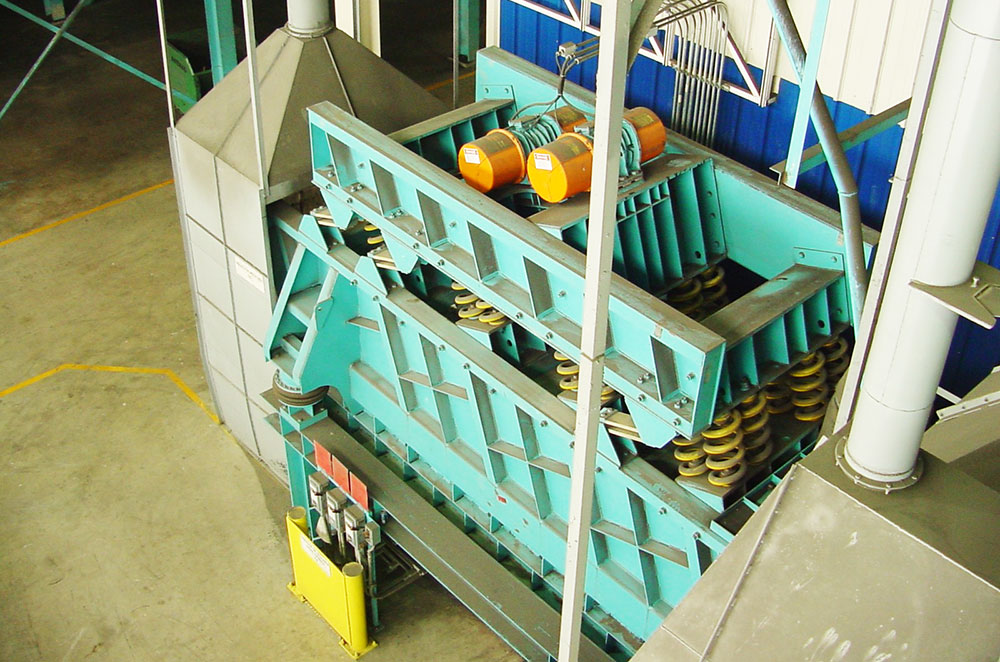
TWO-MASS CONVEYING SHAKEOUT FEEDER
General Kinematics’ high frequency, two-mass shakeouts will boost your foundry throughput. Our unique two-mass design automatically compensates for varying load conditions, assuring non-dampening shakeout performance.
General Kinematics shakeout feeders are specifically designed for your high production molding lines. Capacities range from 30 to 300 tons per hour for gray, ductile or malleable iron. Each shakeout feeder is sized to maintain the proper casting retention time to break down your sand while preventing excessive casting batter.
Two-Mass technology allows the use of variable frequency drives to vary the amount of g-force applied to break down the sand. General Kinematics’ specially designed isolation system allows for incline or decline of the shakeout surface thereby maintaining castings in the shakeout for the desired retention time based on your part number.
FEATURES: The unique GK two-mass design automatically compensates for varying load conditions, assuring non-dampening shakeout performance.
Driven with proprietary sealed vibration shaker motors, GK’s Two-Mass Shakeouts eliminate the need for V-belts, pivoted motor bases, couplings, and large and expensive bearings.
The drive for our shakeout feeders is mounted on a separate exciter mass, completely isolated from the high-intensity impact action of the shakeout deck.
Our vibration shaker units feature low horsepower, adjustable amplitude control, and exceptionally quiet operation.
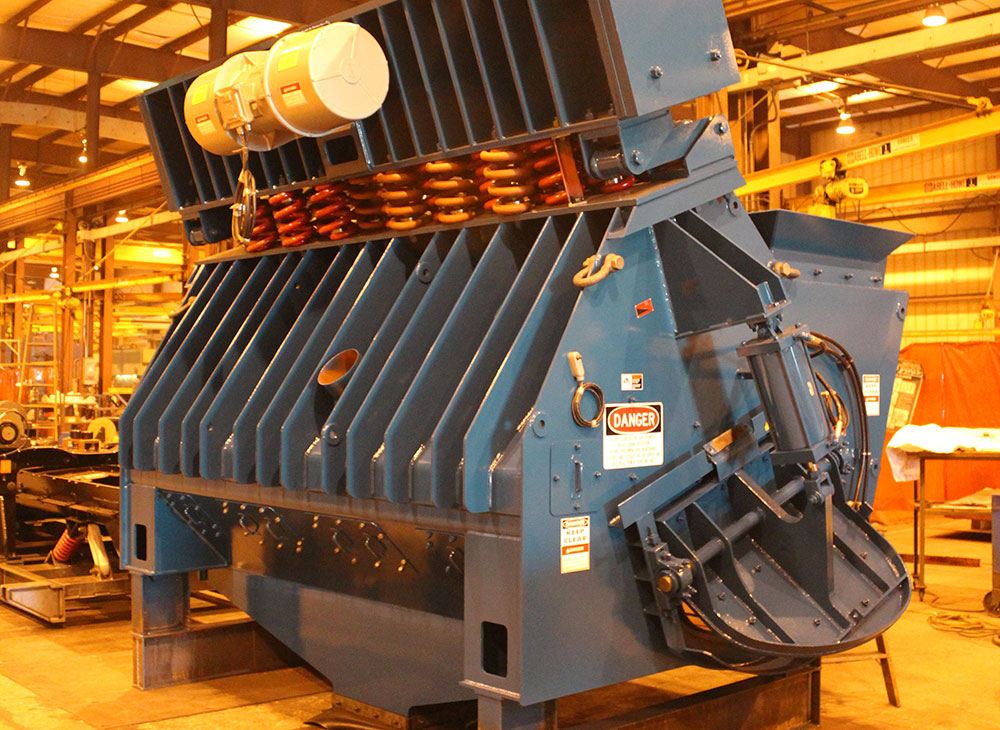
VIBRA-MILL? DRUM: CONTINUOUS-FLOW VIBRATORY SAND RECLAMATION
The VIBRA-MILL? Drum continuous-flow sand reclaimer is designed for continuous and efficient lump reduction of no-bake or chemically bonded sand. The VIBRA-MILL? Drum combines vibration, agitation, tumbling, abrading, and scrubbing for complete and continuous lump reduction to original grain size. Field results show sand reduced 100% minus 20 mesh with original size distribution, and corresponding reduction in L.O.I.
FEATURES:Designed for continuous sand attrition.
Two-mass, low horsepower drive.
Available in custom sizes to match your throughput.
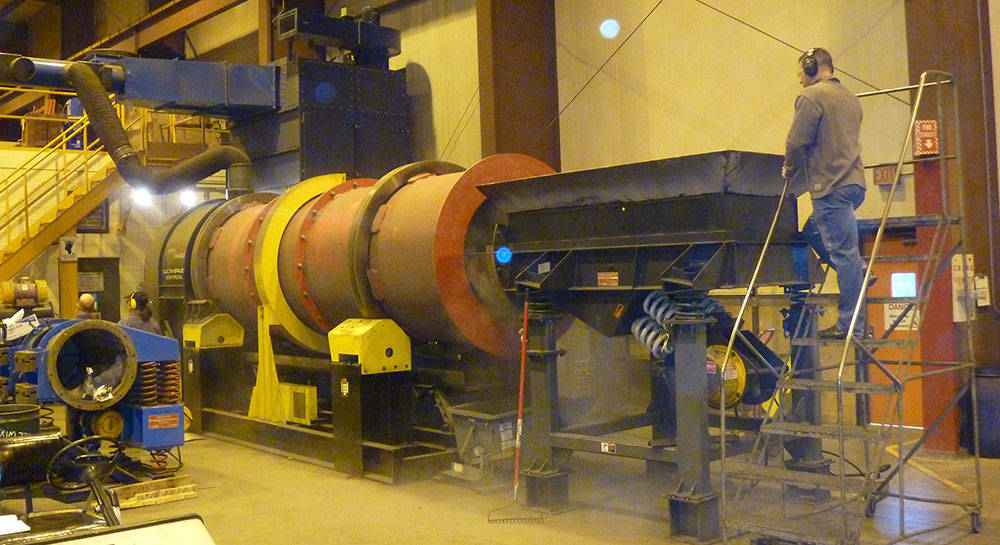
DUCTA-CLAIM? ROTARY LUMP CRUSHER / SAND RECLAIMER
General Kinematics DUCTA-CLAIM? Rotary Sand Reclaimer classifies, separates, crushes, and screens sand for efficient reclamation of sand to grain size. Extra-Heavy duty construction, combined with innovative engineered machine design, gives you a high performance sand reclaimer in a reliable, low maintenance package. The DUCTA-CLAIM? is available in custom lengths, diameters, and throughputs, and can be run as a continuous or batch process.
FEATURES:Classify, separate, crush, and screen sand in one efficient rotary drum.
Available in standard and custom sizes to match your process design and throughput.
Heavy-Duty construction ensures trouble-free operation for maximum uptime reliability.
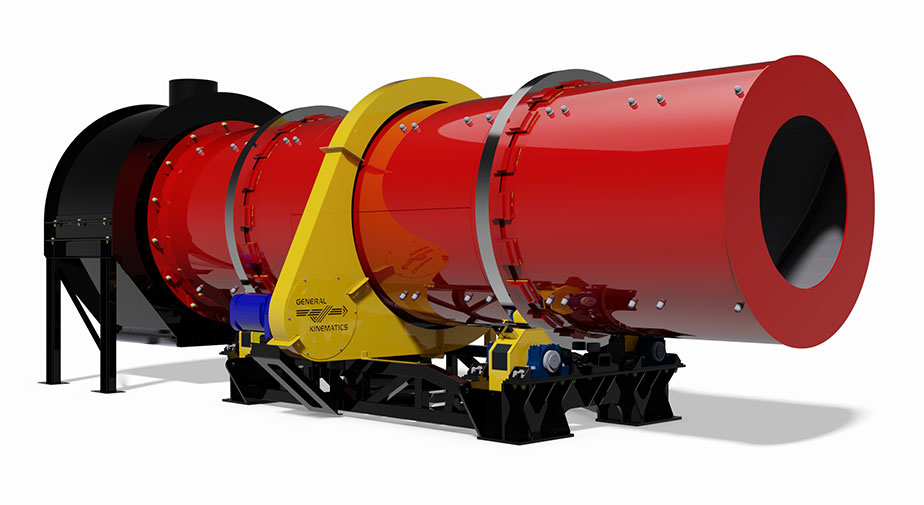
DUCTA-SPRUE? ROTARY SPRUE DRUM
The DUCTA-SPRUE? Rotary Sprue Drum combines innovative patented rotary technology with GK’s proven vibratory material transfer equipment to give you a long lasting, easy to maintain solution for processing sprue, gates, and core butts.
Users report that the direct savings resulting from the cleaning of gates, risers. runners, flash, fins, run-outs and other sprue, before charging them into a melting furnace has repaid the cost of the General Kinematic DUCTA-SPRUE? sprue mill and all accessory feeding and handling equipment in under one year. Charging cleaned sprue into a cupola reduces the required additives in some cases from 4% to less than 1%. This results in substantial savings in coke consumption, faster melting, less slag to handle, reduced deterioration of cupola linings, and easier cupola control. Cores from the shakeout / knockout can be processed with the sprue, releasing rods, gaggers, arbors and wires for picking.
Operation
Material can be loaded into the DUCTA-SPRUE? rotary mill in a variety of ways, then is subject to a tumbling action which removes the sand from the metal and breaks up large core lumps. The sand passes out through slots in the shell while the cleaned metal parts are discharged from the end of the barrel. Air is vented from the screen section, using air drawn in from the inlet and outlet of the barrel to prevent the escape of dust into the foundry.
Standard and Custom Sizes
General Kinematics offer standard as well as custom sized DUCTA-SPRUE? rotary drums. DUCTA-SPRUE? rotary drums employ steeply pitched helical flights at the inlet to advance the material into the cylinder, rapidly avoiding spillage over the feed end retaining ring. The main shell is provided with easy to replace wear resistant liner plates, and lifting bars which raise the material as the shell rotates, increasing the material tumbling effect. The riding rings are forged steel, supported on forged trunnion rollers. Thrust rollers and standard drive equipment are included with all models.
Separation of sand, media, and tramp metal is done outside the rotating assembly on a GK vibratory processor, eliminating rotating mass and wear to the drum body.
GK fabricated liners are easier and safer to replace, and cost up to 75% less than cast grid systems.
Patent-pending liner system eliminates compression rings, heavy cast liners, and excessive maintenance costs.
Drum shell is not a wear item, saving you considerable maintenance funds and headaches.
Drums use easy to source commercially available components.
Available in standard and custom sizes to match your process design and throughput.
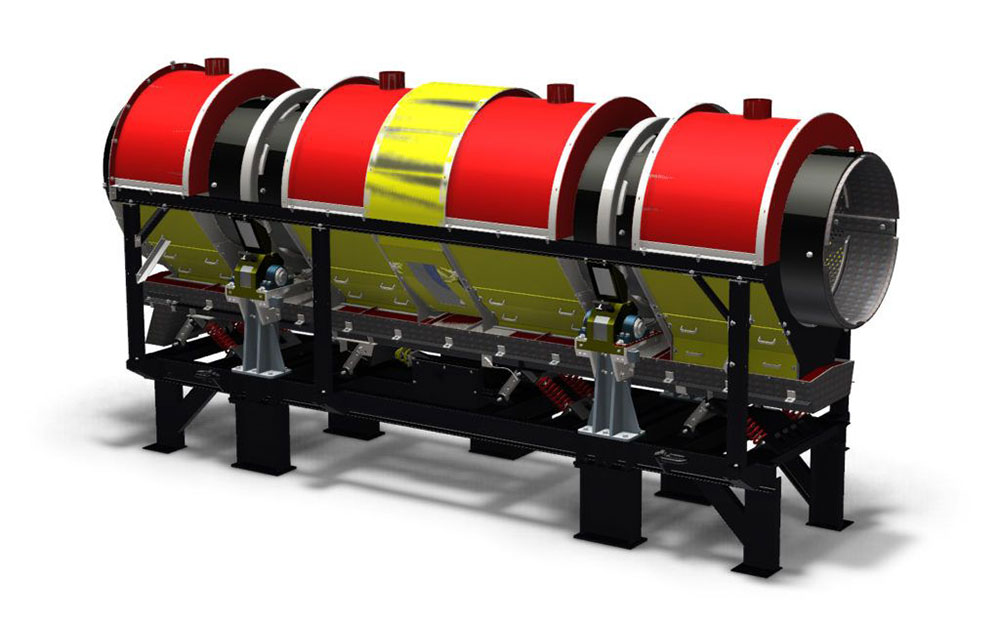
DUCTA-SCREEN? ROTARY SHAKEOUT
The DUCTA-SCREEN? rotary shakeout quickly and efficiently processes molds to separate and remove sand from castings. Sand is broken down, leaves the rotary shell, and is deposited on GK’s vibratory sand take-away conveyor. The removal of sand from the rotary shell allows cooler equipment temperatures, allowing for increased equipment and component life, and reduced casting temperatures.
The DUCTA-SCREEN? rotary shakeout is an ideal unit for separating castings from flaskless molds. The self-contained unit reduces the noise and improves sand separation from castings and sprue. The action of the rotary shakeout is smooth, yet it efficiently breaks down sand lumps and provides sand suitable for very fine final screening. Standard and custom sizes are available to best suit your application.
Contact a GK Foundry specialist for more information.
GK fabricated liners are easier and safer to replace, and cost up to 75% less than cast grid systems.
Patent-pending liner system eliminates compression rings, heavy cast liners, and excessive maintenance costs.
Drum shell is not a wear item, saving you considerable maintenance funds and headaches.
Drums use easy to source commercially available components.
Available in standard and custom sizes to match your process design and throughput.