MELT DECK EQUIPMENT
OPTIMIZE MELT OPERATIONS
General Kinematics melting and sprue cleaning solutions automate your melting operations. From scrap cleaning to furnace charging, GK has a solution to improve the safety and productivity of your melt operations.
CLEANING AND CONVEYING
Returning clean scrap to the melt deck is important to produce a cleaner pour. To get your scrap back, vibratory conveyors from General Kinematics offer quiet, reliable conveying with low maintenance requirements. On the way, GK’s DUCTA-SPRUE? removes sand through aggressive tumbling action and prepares scrap for remelt.
BUILDING YOUR CHARGE
Proper metallurgy is determined even before you melt. GK’s alloy addition, ladle addition, and charge make up solutions automate this process to provide a consistent charge make up every time.
HEAVY-DUTY FURNACE CHARGING
General Kinematics furnace charge feeders are the most reliable and durable vibratory charge feeders available. Each machine is custom engineered for your specific tonnage and furnace type. Feeders are available in a variety of mobile configurations to best fit your facility and process. Combine this with our charge makeup solutions for the ultimate in melt deck performance.
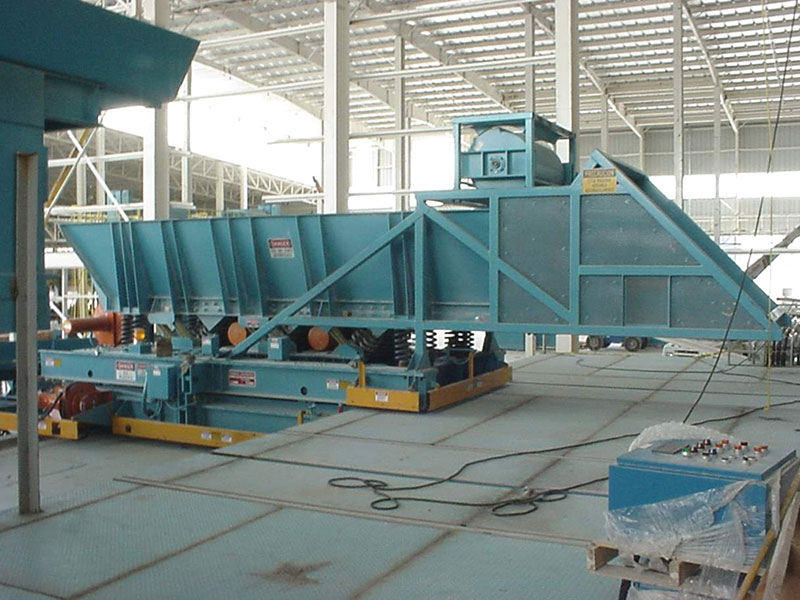
VIBRATING CHARGE FEEDERS
General Kinematics vibrating furnace charge feeders and charge systems give you precise automated batch control, optional scrap drying and other charge enhancement capabilities. Equally important, automated systems help improve worker safety.
Charger nosepiece is designed specifically for your furnace to control fumes and direct the charge into the center of your furnace. Vibrating furnace charge systems can be motorized to move forward, backward, up, down, or transversely as well as full control with wireless weighing.
Patented charge feeder nosepiece expands to prevent jams, fits tight to furnace hood to contain fumes and any potential splashback, and directs charge into center of furnace to reduce furnace damage.
Noise reduction vibrating feeder troughs for quiet furnace feeding.
Heavy duty vibratory feeder designed for 24/7/365 operation with little maintenance requirements reduces your planned downtime.
Two-Mass, natural frequency charge feeder design requires very little energy to operate, reducing your HP and energy costs.
Designed with soft isolation springs that limit transmittal of forces to your furnace deck.
Feeder is designed with a variable speed material discharge to keep your furnace crucible full as material is demanded.
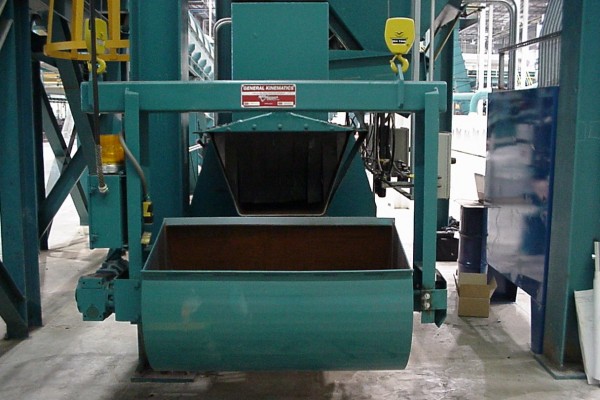
ALLOY / INOCULANT SYSTEMS
General Kinematics Alloy Addition Systems take the guesswork out of your metallurgy. Alloy bins receive and store the ferro-silicone, graphite, or other additions, which is then transferred via vibratory feeder to a main weigh unit for batch make-up. Final batches are delivered to the charge area via delivery barrel and monorail / hoist assembly. Charge feeders are designed to accept and gradually mix alloy batch with the main charge. Fully integrated control systems (SCADA) are included to round out the package.
General Kinematics Inoculant Systems prepare and add inoculants or other materials into the ladle prior to pouring. Systems include individual material bins and feeders, accurate weighing rollovers, charge make-up feeders, and other options to accurately measure and deliver the right mix, in the right order, to your ladle.
FEATURES:
Alloy Addition Systems can be integrated directly with your charge feeder, providing a complete charge solution.
Fully integrated control systems (SCADA) for precise product weighing.
Bins are fed using GK feeders featuring either electromechanical or pneumatic drives, depending on size and application.
Charge make-up feeders utilize weigh cells to accurately measure the correct amount of material for your particular metals mix.
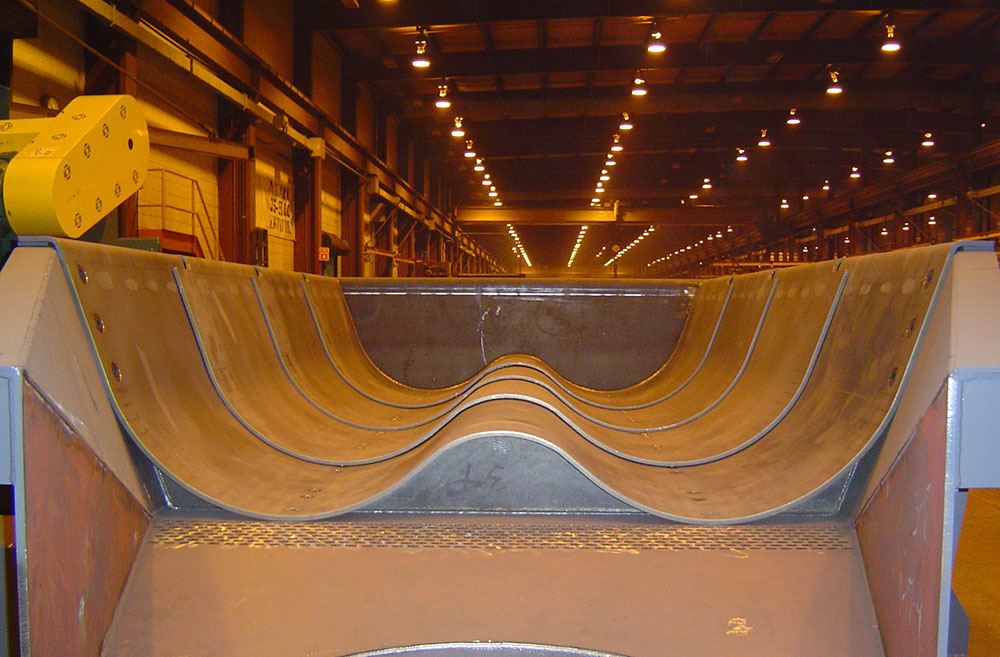
CHARGE PRE-HEAT SYSTEMS
An Integrated Scrap Pre-Heat Process that Increases Furnace Productivity and Reduces Operating Costs
By combining weigh hopper, pre-heat hood, material transfer, and furnace charging into a single automated process, General Kinematics gives your melting operation a new level of cost efficiency.
Pre-heating drives off moisture and other contaminants from the charge material for a safer, more efficient operation. A pre-heated charge reduces induction energy needed to complete the melt, and the resulting shorter melt cycle dramatically increases furnace output. In addition, the use of lower cost natural gas or fuel oil for pre-heating means even higher earnings on your investment dollars.
Adaptable to any size furnace.
Allows use of lower cost wet or oil contaminated scrap.
Efficient drying or heating to 1200 degrees F/650 degrees C for reduced furnace energy demand.
Faster furnace melt cycles.
Flexible layout for any installation.
Single operator, automatic control capability.
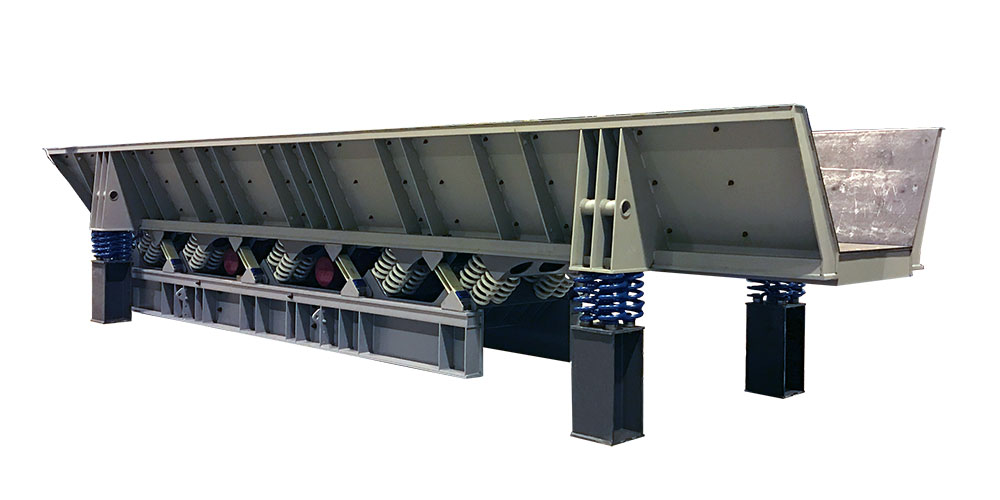
CHARGE MAKE-UP SOLUTIONS
Speed up charge cycles and accurately weigh your charge material with GK’s Charge Make-up Solutions.
With GK’s Charge Make-up Solutions, materials are loaded into either a vibratory feeders or stationary bin with clam-shell bottom gates. Both options are mounted on weigh cells to determine the weight of charge material.
With the vibratory feeder option, multiple units can be arranged in series to separate charge material by type for precise mixing of materials. When system is activated, precise amounts of material are then loaded into the furnace charge feeder for accurate charge make-up. Stationary bins accumulate all material in bin, and when the material mix is correct, clam-shell type gates open, depositing the charge into the furnace feeder.
Selection of which type of charge make-up solution varies by furnace type and specific application. Contact a GK Foundry Specialist for more information.
Accumulate material in scrap yard to decrease charge cycle time.
Accurately measure amount of each type of material to create the correct metallurgy for your charge.
Charge Make-up Solutions are an integral part of GK’s complete furnace charging systems.
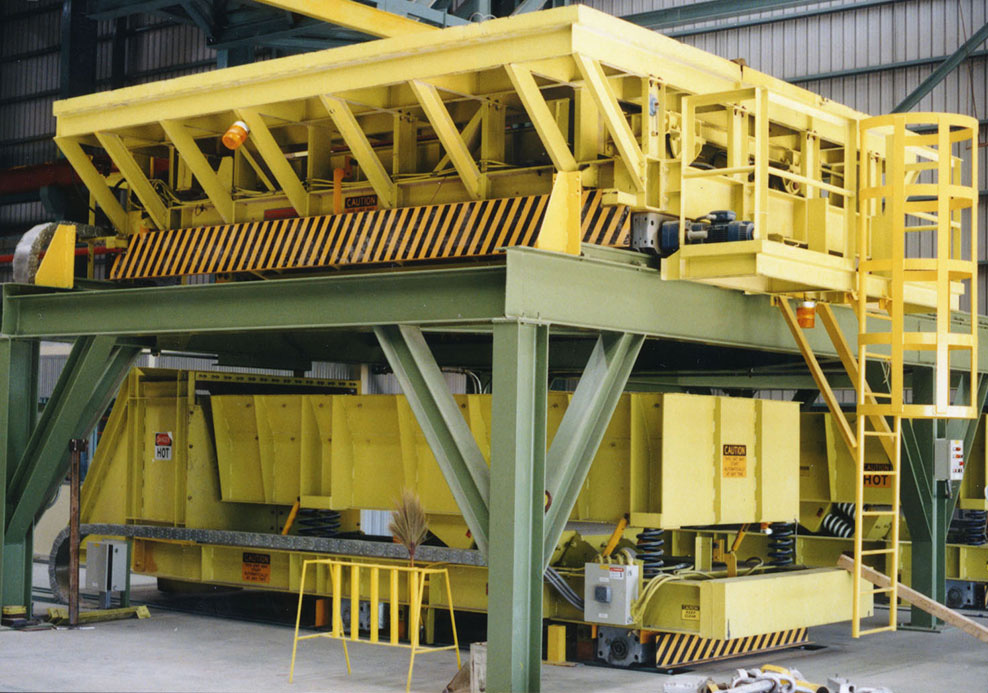
WEIGH HOPPERS
General Kinematics Weigh Hoppers allow the crane operator to pre-weigh and batch scrap recipes as the furnace charge feeder is away from home position charging the furnace. Weigh Hoppers can be stationary or mounted on carriages to transfer your material to a specific location. Can be mounted on your melting department crane or stationary to structure on your melt deck.
FEATURES:Clam-shell gates are pneumatically or hydraulically operated.
Load cell systems integrate with your melt operator recipes.
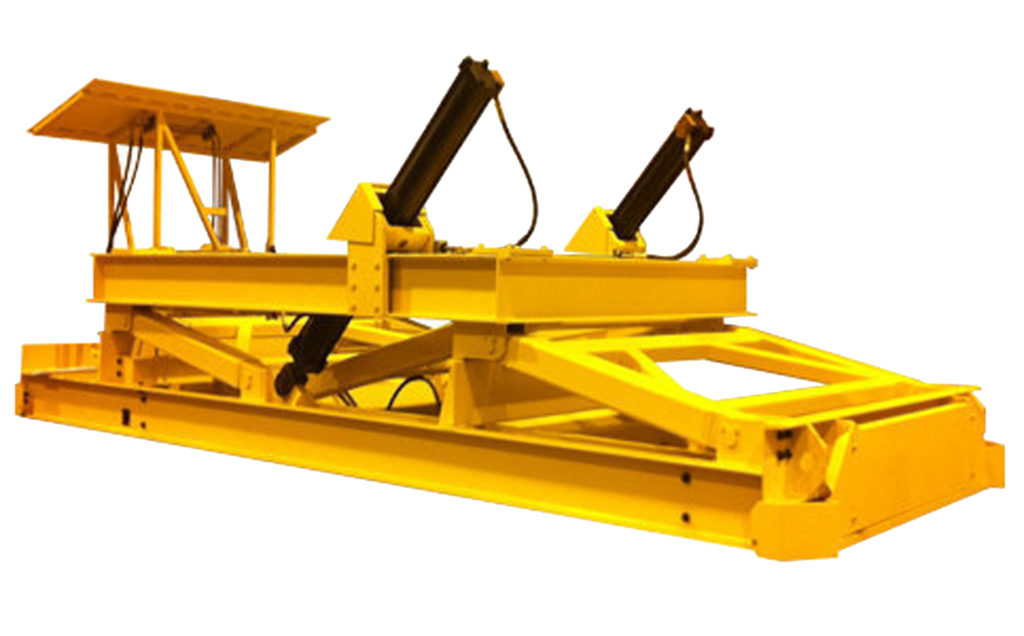
DELIVERY CARRIAGES
Automate your charge area with GK’s mobile delivery carriages.
GK’s delivery carriages transport your vibrating charge feeders from the scrap yard to your furnace. Units can be designed to be rail mounted or fully independent via radio control. Custom designed to fit your specific furnace model, GK can create a delivery carriage that best fits your foundry layout and process.
Carriages automate furnace charge feeders, allowing them to have index, traverse or pivoting movement from your scrap loading area to the furnace.
Safety sweeps mounted around the carriage frame safely stop units if something is in the carriage path.
Integrated safety alarms and lights alert workers to carriage movement.
Easily integrated into control system for seamless process operations.
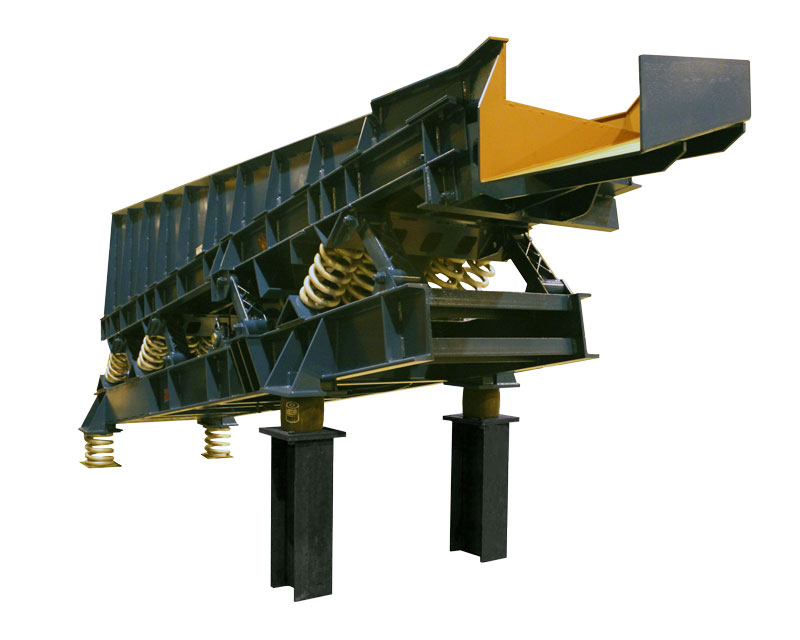
DRY / WET SLAG COOLING CONVEYOR
General Kinematics Dry Slag Cooling Conveyor eliminates popcorn slag, slag pans, and apron conveyors. With GK’s Dry Slag System, slag is conveyed, cooled indirectly, and transformed into a semi-solid pancake slag. The patented indirect cooling trough technology of the Dry Slag Cooling Conveyor means slag can immediately be containerized or discharged to a quench tank. Units are available in custom widths and lengths to fit your process. With GK’s dry slag technology, customers receive a solidified aggregate slag which can provide beneficial reuse and eliminate filling landfills.
General Kinematics Wet Slag Conveyors were originally designed and patented by General Kinematics in the late 70’s, and are still the most rugged machine for quenching slag, dross, castings, and other hot metal and metal by-products. General Kinematics vibratory Wet Slag Conveyors combine a water reservoir within a vibratory feeder to provide you with a clean and effective way to quickly cool slag or other hot materials. GK Wet Slag Conveyors accept hot material directly, instantly quenching the material. The molten slag is quenched and cooled in the water bath creating popcorn slag which is then conveyed out and ready for immediate disposal.
For more information on Dry Slag or Wet Slag Conveyors, contact a GK foundry expert.
Process eliminates “popcorn” slag commonly seen in other water quenching processes.
Creates granular material that can be used for aggregate in other industries.
Utilizes GK’s patented indirect cooling trough technology to consistently maintain product temperature.
Custom designed to fit your process and space constraints.
WET SLAG CONVEYOR FEATURES:
Vibratory action conveys post-quench material to a container or further processes while retaining the water bath in the trough.
Closed loop water system is clean and easy to maintain. New water is added only to compensate for loss through evaporation.
Vibratory conveyor is balanced and isolated to minimize vibration transmission and foundation requirements.
Designs available with customized drives and troughs to meet your elevation requirements.
Standard features include stainless steel trough construction and bolted wood plank inlet for maximum protection against corrosion and molten contact wear.
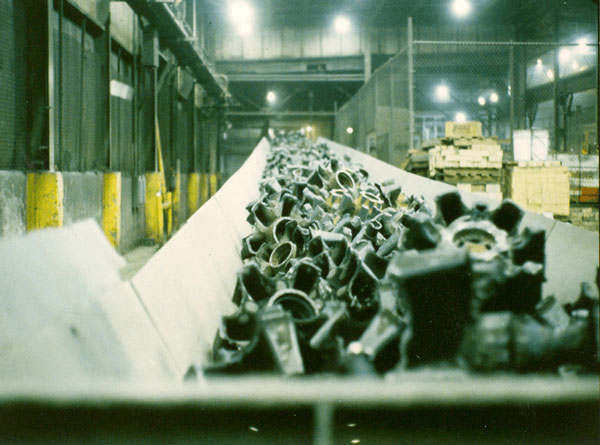
SYNCRO-COIL? VIBRATING CONVEYORS
General Kinematics SYNCRO-COIL? Vibratory Conveyors are designed for the extreme environment of foundry operation. Conveyors feature rugged long life components and heavy-duty construction, and are designed specifically for your material and process.
Trough Design
Recommending the correct trough design is one of the most important factors in meeting your needs for vibratory conveyors. It’s not just fit and finish; our experienced design staff gives careful considerations to product factors such as bulk density, angle of repose, particle size and configuration to name just a few. Further, we offer trough designs with sub-assemblies that speed up trough replacement for high wear applications.
SYNCRO-CUSHION? Coil Spring Drive
Our proven SYNCRO-CUSHION? coil spring drive combines the advantages of natural frequency vibratory action with a rugged drive and trough connection. The result: exceptional performance in high load or adverse operating conditions.
Available in infinite lengths and widths.
Each machine is designed specifically for your application so you know it will work.
SYNCRO-COIL? drive system uses very little energy and can power through adverse operating conditions.
Conveyors can go up, down, or in circles.